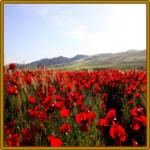
سلام به وب من خوش آمدید دوستان و همراهان عزیز از اینکه مهمان این وب هستید بسیار سپاسگزارم منتظر نظرات سازنده ی شما دوستان هستم
عنوان | پاسخ | بازدید | توسط |
![]() |
1 | 1216 | piskesvat |
![]() |
3 | 2710 | mehran99 |

تاريخچه :
فرآیند رسوب سختی (پیرسختی) در سال 1906 بوسيله Dr.A.Wilmآلمانی کشف گردید.دكتر Wilm یک آلیاژ 4 درصد مس و 5/0 درصد منیزیم را حرارت داده و پس از آن به سرعت سرد نمود و سپس سختی آلیاژ را اندازه گرفت. او متوجه شد که با گذشت زمان به مدت چند روز در درجه حرارت محیط سختی نمونه ها به مقدار قابل ملاحظه ای افزایش یافت.
دكتر Wilm در سال 1911 نتایج خود را منتشر نمود ولی نتوانست توضیحی برای این سخت شدن بدهد. زیرا از نظر میکروسکوپی هیچ گونه تفاوتی بین نمونه های سخت و نمونه های نرم مشاهده نکرده بود. از زمان Wilm تا کنون دانشمندان و مهندسین متعددی فرآیند رسوب سختی را مطالعه و مطالب مختلف و متعددی در مورد آن یافته اند ولی هنوز هم مکانیزم دقیق آن مورد مطالعه قرار می گیرد.
اصول رسوب سختی:
برای سخت کردن یک آلیاژ آلومینیوم از طریق فرآیند رسوب سختی ابتدا به فلز یک عمل حرارتی حل کردن داده می شود عمل حرارتی آلیاژ را به درجه حرارتی که بقدر کافی زیاد است تا عناصر آلیاژی را داخل محلول جامد بنماید حرارت می دهند.
درجه حرارت مورد استفاده بستگی به ترکیب شیمیائی آلیاژ دارد. پس از حرارت دادن به درجه حرارت انحلال و نگه داشتن در آن درجه حرارت به مدت لازم آلیاژ به درجه حرارت پائین تری سریعاً سرد می شود تا این عناصر را در محلول جامد فوق اشباع شده نگه دارد.
قسمت دوم فرآیند رسوب سختی، پیر کردن است که در خلال رسوبات تشکیل می گردند. اگر رسوب گیری که باعث سختی آلیاژ می شود خود به خود در درجه حرارت محیط انجام گیرد گفته می شود که آلیاژ بصورت طبیعی پیر شده(Natural Ageing) است.
در هر حال اگر لازم باشد آلیاژ را حرارت داد (معمولاً در 260-93 درجه سانتی گراد به مدت چندین ساعت) تا رسوب گیری انجام گیرد در آن صورت آن را پیر سختی مصنوعی(Artificial Ageing) مي نامند.
آلیاژهای آلومینیوم که قابل سخت شدن از طریق رسوب سختی هستند را بنا به تعریف آلیاژهای عملیات حرارتی پذیر می نامند.
شرایط مورد نیاز:
برای این که آلیاژ آلومینیوم قابل رسوب سختی باشد باید برخی شرایط خاص را دارا باشد. اول این که آلیاژ باید حاوی مقادیرقابل توجهی از حداقل یک عنصر یا یک ترکیب که با کاهش درجه حرارت از حد حلالیت حالت جامد آن کاسته می شود باشد یعنی این عناصر یا ترکیبات باید دارای حلالیت حالت جامد قابل توجهی در درجات حرارت بالا و حلالیت حالت جامد ناچیز در درجات حرارت پائین باشند.
شرط دوم این است که عنصر یا ترکیبی که در محلول جامد فوق اشباع نگه داشته می شود باید رسوب کرده و تولید تغییر فرم ها و اعوجاج شبکه ای در آلومینیوم بنماید. معمولاً رسوب این عناصر یا ترکیبات بتدریج باعث سخت تر شدن آلیاژ شده تا این که سختی آن به یک مقدار حداکثر برسد. ادامه عملیات رسوب گیری پس از این نقطه باعث کاهش سختی می گردد.آلیاژهائی که به مقدار کافی پیر نشده و به سختی حداکثر نرسیده باشند را کم پیری(underaged)و آلیاژهائی که از سختی حداکثر رد شده باشنديا بمدت طولانی تر پیر شده باشند را پرپیری(overaged)می نامند .
فرایند رسوب سختی آلیاژهای آلومینیوم را می توان بصورت زیر خلاصه نمود:
1-گرم کردن به درجه حرارت عملیات حرارتی انحلال (حل کردن)
2-حرارت دادن در آن درجه حرارت برای مدت زمان کافی
3- سريع سرد كردن به درجه حرارت نسبتا پايين
4-پیر کردن برای رسوب سختی از طریق:
v الف- پیرکردن طبیعی در درجه حرارت محیط یا،
v ب- پیر کردن مصنوعی بوسیله حرارت دادن در یک درجه حرارت پائین260-93 درجه سانتی گراد بمدت لازم.
به عنوان مثال عملیات حرارتی یک آلیاژ AL -cu 4% را در نظر بگیرید. ابتدا آلیاژ به 504 درجه سانتی گراد حرارت داده می شود تا تمام مس وارد محلول جامد گردد. سپس آلیاژ در آب سرد سریعاً سرد می گردد تا به درجه حرارت محیط برسد. اگر آلیاژ به 171 درجه سانتی گراد بمدت ده ساعت حرارت داده شود از طریق پیر کردن مصنوعی سخت می گردد. باید توجه داشت که اگر این آلیاژ حاوی 5/0 درصد منیزیم باشد می تواند در درجه حرارت محیط بصورت طبیعی پیر سخت شود.
1-عمل حرارتی انحلال (Solution Heat Treatment):
درجه حرارت عملیات حرارتی انحلال طوری انتخاب می گردد که بالاتر از منحنی حلالیت جامد باشد ولی خطر ذوب اجزاء یوتکتیکی نقطه ذوب پائین وجود نداشته باشد. معمولاً کنترل درجه حرارت کروه در حدود دقت 5/5+ درجه سانتی گراد نگه داشته می شود. آلیاژهائی که حتی چند درجه بیشتر از حد معین حرارت داده شوند بطور جزئی ذوب شده و در آن صورت فلز مربوطه را باید به علت از دست دادن خواص مکانیکی بصورت قراضه و ضایعات در آورد.
زمان لازم برای عملیات حرارتی انحلال بستگی به آلیاژ و نوع محصول دارد. بطور کلی قطعات کار شده احتیاج به زمان کمتری نسبت به قطعات ریختگی داشته و قطعات کار سرد شده زمان کمتری نسبت به قطعات کار گرم شده دارد. قطعات در ماسه به علت درشت بودن اجزاء ساختمانی آنها زمان بیشتری نسبت به قطعات ریختگی در قالب دائمی دارد. در مورد اغلب محصولات صفحه ای ورق، نیم ساعت تا دو ساعت زمان کافی برای عملیات حرارتی انحلال است، از طرف دیگر برخی از قطعات ریختگی ممکن است تا 12 ساعت حرارت دادن نیاز داشته باشند. اگر ماده کار سرد شده باشد باید آن را تقریباً به سرعت به درجه حرارت انحلال لازم رسانید تا از رشد دانه ها جلوگیری گردد.
باید به تفاوت بین عملیات حرارتی انحلال و عملیات تا بکاری کردن توجه شود. در هر دو مورد فرآیندهای بازیابی، تبلور مجدد و رشد دانه بطور مشابه انجام می گیرد. در هر حال عملیات حرارتی انحلال نسبت به عملیات تابکاری در درجه حرارت بالاتری انجام می شود تا به اجزاء ساختمانی لازم چون اجازه انحلال و ورودی به محلول جامد داده شود، که پس از آن رسوب می کند. در تابکاری قطعات، این اجزاء ساختمانی به مقدار زیادی وارد محلول جامد نمی گردد ولی اجازه رشد و درشت تر شدن ذرات داده می شود. قطعات عمليات حرارتی انحلال شده نسبت به قطعات تابکاری شده، به علت استحکام بخشی از طریق محلول جامد حاصل، معمولاً سخت تر هستند.
2- سریع سرد کردن (Quenching) :
پس از این که اجزاء ساختمانی وارد محلول جامد گردیدند آلیاژ آلومینیوم به سرعت به درجه حرارت پائینی سرد می شود تا این اجزاء در محلول باقی بمانند. معمولی ترین محیط های سرد کردن آلیاژهای آلومینیوم آب داغ و آب سرد است.
سریع سرد کردن در آب سرد برای مواد نازکی چون ورق، قطعات فشار کاری شده، لوله و قطعات پتکاری شده کوچک بکار می رود. درجه حرارت آب زیر 29 درجه سانتی گراد نگه داشته می شود و اجازه افزایش بیش از 11 درجه سانتی گراد به آن داده نمی شود. این سرد شدن ناگهانی حداکثر مقاومت در مقابل خوردگی را به آلیاژ می دهد ولی ممکن است باعث اعوجاج قطعه گردد. عموماً پس از سریع سرد کردن در آب سرد نمونه را صاف می کنند تا هر گونه چین و چروک و عیوب دیگر از این نوع را حذف نمایند. سریع سرد کردن در آب داغ بر روی قطعات سنگین آلومینیومی چون قطعات بزرگ پتکاری شده و ریختگی که در مورد آنها مقاومت خوردگی زیاد مهم نیست بکار می رود. سریع سرد کردن در آب داغ عموماً در 66 درجه سانتی گراد تا 82 درجه سانتی گراد و یا در 100 درجه سانتی گراد (آب جوش) انجام می گیرد. چون سرد کردن در آب داغ آهسته تر از سرد کردن در آب سرد است بنابراین اعوجاج قطعه در این مورد خیلی زیاد نبوده و به مقدار حاصل در آب سرد نیست.
3-پیرسازی (Ageing) :
آلیاژهای آلومینیوم پس از عملیات حرارتی انحلال و سریع سرد کردن پیر می شوند تا رسوب دهند. سریع سرد کردن از درجات حرارت بالا قسمت اعظم عناصر محلول را در درجات حرارت پائین در داخل محلول جامد فوق اشباع نگه می دارد. در هر حال آلیاژهای آلومینیوم قابل سخت شدن از طریق رسوب گیری در حالت سریع سرد شده ناپایدار هستند. در اثر پیر شدن، ذرات بسیار ریز میکروسکوپی تشکیل می گردند که به عنوان مانع در دانه ها و مرزدانه ها عمل می نمایند. این ذرات بسیار ریز پخش شده در آلیاژ بقدری به آن استحکام می بخشند که آلیاژ می تواند بار بیشتری را تحمل کرده و تغییر فرم بیشتری را بدست آورد. اندازه و چگونگی توزیع رسوب بسیار مهم است زیرا ذرات بسیار درشت باعث ایجاد خواص مکانیکی ضعیف تر از خواص مکانیکی مطلوب می گردند. آلیاژهای آلومینیوم قابل پیر شدن طبیعی استحکام کامل خود را پس از 4 تا 5 روز در درجه حرارت محیط بدست می آورند. در حدود 90 درصد حداکثر استحکام قابل حصول در این آلیاژها پس از 24 ساعت حاصل می گردد. شکل دادن آلیاژهای قابل پیر سختی طبیعی عموماً در حالت نرم قبل از پیر سختی انجام می گیرد. با قرار دادن قطعات درست پس از سریع سرد شدن و قبل از پیر سختی طبیعی یافتن دریخ خشک73تا 46 درجه سانتی گراد می توان از رسوب گیری جلوگیری نمود تا قطعه در زمان لازم مورد استفاده قرار گیرد. پیر سختی مصنوعی آلیاژهای آلومینیوم عموماً در درجات حرارت 260-93 درجه سانتی گراد انجام می گیرد وقت درجه حرارت در حد 3 + درجه سانتی گراد نگهداشته می شود. زمان لازم برای عمل بستگی به آلیاژ و درجه حرارت پیرسختی دارد وقتی که یک آلیاژ جدید ساخته شد در درجات حرارت و برای مدت زمان های مختلف منحنی های پیر سختی تجربی رسم می گردد تا مشخصات پیر سختی مناسب بدست آید.
رسوب سختی آلیاژهای کار پذیر آلومینیوم:
رسوب سختی در برخی از انواع مهم سیستم های آلیاژی آلومینیوم در اینجا مورد بررسی قرار می گیرد. برای درک بهتر باید به نمودارهای تعادلی که در فصول قبلی آورده شده است نیز مراجعه شود.
1-آلیاژهای Al-Cu :
همان گونه که ذکر گردید فرآیند رسوب سختی برای اولین بار بوسیله wilm در آلیاژ آلومینیوم حاوی 5/4 درصد مس و 5/0 درصد منیزیم مشاهده گردید. به این دلیل سیستمAl-Cu-Mg سیستمی است که مورد بررسی و تحقیق زیاد قرار گرفته است.
مکانیزم رسوب دادن ذرات :
1- عمليات حل سازي درمنطقه محلول جامدآلفا انجام شود(حدود 515 درجه سانتي گراد) :
ابتدا آلياژآلومينيوم با 4% مس بايد تا حدود 515 درجه سانتي گراد گرم شود تا اينكه اتم هاي مس و آلومينيوم به طور تصادفي به داخل محلول جامد همگن آلفا نفوذ كند. آلياژ در اين مرحله از محلول جامد آلفا تشكيل شده است.
2- تا دماي اتاق يا كمتر به سرعت آبدهي شوند:
اين عمليات يك محلول جامد فوق اشباع مس در آلومينيوم ايجاد ميكند. آلياژآلومينيوم با 4% مس در اين شرايط پايدار نيست و سعي ميكند با ساختن فازهاي نيمه پايدار انرژي سيستم را كاهش دهد.نيروي محركه فازهاي نيمه پايدار،انرژي زياد محلول جامد فوق اشباعنا پايدار مس در آلومينيوم است.
3- در گستره دمايي 130 تا 190 درجه سانتي گراد به طور مصنوعي پير شوند:
اگر چه برخي از آلياژ ها در دماي اتاق تا استحكام مورد نظر پير سخت مي شوند، ولي اغلب آلياژها بايد در دماي بيشتر پير شوند. در مورد آلياژ آلومينيوم با 4% مس دماي پير سختي مصنوعي بين 130 تا 190 درجه سانتي گراد است.
ساختار هايي كه به هنگام پيرشدن آلياژهاي آلومينيوم مس تشكيل مي شوند عبارتند از :
الف : محلول جامد فوق اشباع .
ب : مناطق GP1 .
پ : مناطق GP2 ( يا فاز "θ).
ت : فاز 'θ.
ث : فاز θ.
ب : مناطق GP1 :
اين مناطق در دما هاي پايين تشكيل مي شونديعني كمتر از 130 درجه سانتي گراد ، و با جدايش اتمهاي مس در محلول جامد فوق اشباع آلياژهايآلومينيوم مس بوجود مي آيند. مناطق GP1 شامل ديسكهايي به ضخامت 4 تا 6 آنگستروم و قطر 80 تا 100 آنگستروم است كه بر سطوح مكعبي {100} زمينه ساخته مي شوند. طبق نظريه دالگرين مناطق GP1 درصد كمي مس دارد. مناطق GP1 با ميكروسكوپ الكتروني قابل مشاهده ميباشد. اين مناطق از حركت نابجاييها جلوگيري مكنند و باعث كاهش شكل پذيري و افزايش استحكام مي شوند.اين مناطق بدليل آنكه قطر اتمي مس حدود 11 درصد كمتر از آلومينيوم بوده پارامتر شبكه مكعبي منطقه كمتر از شبكه زمينه است و در نتيجه به صورت تتراگونال كشيده مي شود.
پ : مناطق GP2 ( يا فاز "θ) :
مثلمناطق GP1 ، مناطق GP2 نيز ساختاري تتراگونال دارند و با صفحات {100} زمينه آلومينيوم با 4% مس يا آلياژ هاي مشابه همدوس هستند. در مراحل اوليه تشكيل مناطق GP2 به نظر مي رسد كه مقدار مس كم است ولي با افزايش زمان پير شدن هم مقدار مس و هم اندازه رسوب ها افزايش مي يابد. قتي كه پير شدن در دماي 130 تا 190 درجه سانتي گراد انجام شود مناطق GP2 سختي آلياژ آلومينيوم با 4% مس را بيشتر افزايش مي دهد .
ت : فاز 'θ :
فرا پيري آلياژ آلومينيوم با 4% مس زماني رخ مي دهدكه فاز كاملا نامربوط ، نا همدوس و نيمه پايدار 'θبه وجود آيد.اين فاز به صورت ناهمگن مخصوصا روي نابه جايي ها جوانه مي زند. اندازه فاز 'θ به مدت زمان و دماي پيري بستگي دارد . وقتي اين فاز به تنهايي ظاهر شود آلياژ در فرا پيري است.
ث : فاز θ :
پير كردن در دماي 190 درجه سانتي گراد يا بيشتر براي مدت خيلي طولاني فاز تعادلي نا همدوس 'θ، Cu Al2 را ايجاد مي كند .اين فاز داراي ساختار BCT بوده و وقتي كه آلياژ در شرايط فرا پيري شديد باشد بوجود مي آيد. فاز θ با از بين رفتن فاز 'θبوجود مي آيد.
-2آلیاژهای Al-Mg-Si:
همان گونه که قبلاً گفته شد جزء اصلی سخت کننده در این آلیاژها است که به مقدار یک تا دو درصد موجود است. حد حلالیت جامد در درجه حرارت یوتکتیک در حدود 85/1 درصد بوده به تدریج با کاهش درجه حرارت به تا درجه حرارت محیط به حدود 1/0 درصد کاهش می یابد. مکانیزم رسوب گیری هنوز موردشک و تردید می باشد ولی اعتقاد بر این است که رسوبات بصورت رشته های کوچکی رسوب می کنند که بعداً بصورت ورقه های کوچک رشد می نمایند.
این آلیاژها عموماً در 521 درجه سانتی گراد عملیات حرارتی انحلال می شوند، ولی در واقع استحکام آنها با افزایش درجه حرارت عملیات حرارتی انحلال به تا 522 درجه سانتی گراد افزایش می یابد. برای پرهیز از بیش از حد داغ شدن و ذوب در عملیات تجارتی از درجات پائین تر از 521 درجه سانتی گراد استفاده می شود. برای حصول حداکثر استحکام، آلیاژهای Al-Mg-Si باید از درجه حرارت عملیات حرارتی انحلال سریعاً سرد شوند. این آلیاژها بصورت طبیعی پیر نمی شوند زیرا درجه حرارت محیط خیلی آهسته و بتدریج پیر سخت می گردند.
چون پیر شدن طبیعی برای مدت زمان کوتاه تولید استحکام بقدر کافی و پایداری نمی کند بنابراین برای آلیاژهای تقریباً همواره از پیر کردن مصنوعی استفاده می گردد. پیر کردن در درجات حرارت پائین تر و برای مدت زمان های طولانی تر بالاترین استحکام را ایجاد می نماید. آلیاژ 6061 معمولاً از طریق عملیات حرارتی انحلال، سریع سرد کردن و پیر سختی مصنوعی ساخته می شود.
-3آلیاژهای : Al-Zn-Mg-Cu
روابط تعادلی در درجات حرارتی مختلف برای سیستم Al-Zn-Mg-Cu قبلاً مورد بررسی قرار گرفته بود. مهمترین فازهای رسوبی که باعث سختی می شوند و می باشند. ذرات در این آلیاژها که حاوی روی بیشتری نسبت به منیزیم هستند موثر تر می باشند .بنظر می رسد که رسوب گیری در آلیاژهای Al-Zn-Mg بصورت زیر انجام می گیرد :
←فاز واسطه ←مناطق .G.P.در آلومینیم
با افزایش مس به آلیاژهای Al-Zn-Mg فازهای تشکیل می شود ولی به نظر می رسدکه در انیجا نیز فاز اصلی سخت کننده رسوبات باشند.
چون این آلیاژها دارای یوتکتیکهای نقطه ذوب پایینی هستند باین جهت آنها را در 477-443 درجه سانتی گراد عملیات حرارتی انحلال می نمایند.چگونگی پیر سختی آلیاژ7075 در درجه حرارت محیط و18-درجه سانتی گراد در شکل 16 نشان داده شده است.مانند آلیاژهای Al-Cu می توان با نگهداشتن این آلیاژها در درجات حرارت پایین ،پیر سخت شدن طبیعی آنها را به تأخیر انداخت . آلیاژ 7079 دارای مشخصات پیر سختی طبیعی مشابه 7075 بوده ولی استحکام کمتری در این آلیاژ تولید می شود
پیر سخت شدن طبیعی آلیاژهای Al-Zn-Mg-Cu گرچه باعث افزایش استحکام می گردد ولی تولید فلز ناپایداری کرده وبنا براین این آلیاژها فقط به حالت پیر سخت شدن مصنوعی مورد استفاده قرار می گیرند.منحنی های پیر سختی مصنوعی آلیاژ 7075 که در ان پیر سختی از 17 روز پس از سریع سرد شدن آلیاژ از درجه حرارت عملیات حرارتی انحلال شروع شده است
منبع:h-daneshmand.ir