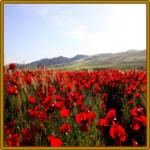
سلام به وب من خوش آمدید دوستان و همراهان عزیز از اینکه مهمان این وب هستید بسیار سپاسگزارم منتظر نظرات سازنده ی شما دوستان هستم
عنوان | پاسخ | بازدید | توسط |
![]() |
1 | 1216 | piskesvat |
![]() |
3 | 2712 | mehran99 |

۱-ماسه قالب گیری
بیشتر ماسه ای مورد استفاده در ریخته گری آلومینیم از ذرات شن، مواد چسبی رسی و رطوبت تشکیل گردیده است. ماسه طبیعی ( که دانه بندی آن در طبیعت انجام شده است) با مقدار مناسب چسب رسی را ماسه ریخته گری طبیعی می نامند. برخی ماسه ها را با افزودن چسبهای خاکی (بنتونیت)به ماسه طبیعی یا ماسه سنگ خرد شده می سازند که به آن ماسه های مصنوعی می گویند.
ماسه قالب گیری باید دارای قابلیت شکل پذیری خوب باشد، یعنی ماسه باید به آسانی اطراف مدل را پر کند. لایه های ماسه نیز باید بحد کافی بهم بچسبد طوری که پس از خارج کردن مدل و در جریان بارریزی، قالب شکل خود را حفظ کند. این خاصیت ماسه را استحکام تر می نامند. دانه های ماسه باید بحد کافی فضای خالی برای خروج گاز و بخار از قالب را تولید نماید. این خاصیت را نفوذ پذیری یا قابلیت نفوذ می نامند. نفوذ پذیری باید در تعادل با تراکم که برای تولید مشخصات دقیق سطحی قطعه لازم است باشد. چند نمونه از خواص ماسه های طبیعی و مصنوعی در جدول ۲-۵ داده شده است.
ماسه های طبیعی برای تولید سطوح صافتر ترجیح داده می شوند زیرا این ماسه ها معمولاً حاوی دانه های شن ریزتری می باشند ماسه های مصنوعی معمولاً با بنتونیت که یک ماده رسی است بهم چسبیده می شوند و نفوذ پذیری بالاتری نسبت به ماسه طبیعی از خود نشان می دهند.
۲-ماهیچه های ماسه ای
منظور از بکار بردن ماهیچه (شکل ۳-۵) تشکیل یک قسمت توخالی در قطعه ریختگی است. معمولی ترین نوع ماهیچه مورد استفاده برای قطعات ریختگی آلومینیم از مخلوطی از ماسه های سیلیکا یا ماسه ساحلی، مواد چسبنده و آب تشکیل شده است. مواد چسباننده مورد استفاده از نوع روغنهای نباتی، مشتقات نفتی، رزینها، حبوبات، پروتئین ها، زفت (محتوی قیر و مواد رزینی و از بقایای تقطیر) ویا ترکیبی از این مواد است.
پس از اینکه ماهیچه قالب گیری شد پخته می شود تا رطوبت خود را از دست داده و مواد چسبان خود را بگیرند. پختن معمولاً در (۴۵۰-۳۵۰ درجه فارنهایت) ۲۳۲-۱۷۷ درجه سانتی گراد انجام می گیرد زیرا درجه حرارت خیلی زیاد باعث پائین آوردن استحکام می گردد. برای ساختن ماهیچه های خوب مقدار رطوبت، استحکام تر و پخته، نفوذپذیری پخته، فشار خشک، سختی سطحی و قابلیت جمع شدن آن باید دقیقاً کنترل شود. برای اجتناب از ایجاد سوراخ در قطعه باید خروج گازهای ماهیچه در حداقل مقدار نگهداشته شود. بطور خلاصه ماهیچه پخته باید دارای قابلیت نفوذ پذیری زیاد در مقابل گاز و مسیر گازی خوب بوده و در تماس با مذاب آلومینیم بحد کافی محکم باشد و پس از انجماد بحد کافی استحکام خود را از دست بدهد تا به آسانی از قطعه جدا شود.
در یک روش دیگر برای ساختن ماهیچه ها، پختن حذف شده و ماهیچه هائی با تلرانس ابعاد دقیق تر ساخته می شود. این روش شامل استفاده دی اکسید کربن برای سخت کردن یک مخلوط ماهیچه از سیلیس و سیلیکات سدیم است. واکنش سخت کنندگی CO۲ ماهیچه
Na۲ Sio۳+ CO۲ = Na۲CP۳+Sio۲
علاوه بر واکنشهای فوق ماهیچه ها را می توان بوسیله یک روش پوسته ای که در آن به عنوان مثال ماسه ای که بوسیله رزین بهم چسبیده است بصورت یک پوسته نیز تولید نمود. برای ساختن این ماهیچه پوسته ای، ماسه همراه رزین بداخل یک جعبه ماهیچه فلزی داغ تزریق می گردد. پس از چند ثانیه مقدار اضافی خارج شده و یک ماهیچه پوسته ای باقی می ماند، روش قالب گیری پوسته ای بعدا در این فصل مورد بررسی قرار خواهد گرفت.
ریخته گری در قالب دائمی
در ریخته گری در قالب دائمی، آلومینیم بداخل یک قالب فولادی یا چدنی که برای تولید تعداد بسیار زیادی قطعه مورد استفاده مجدد قرار می گیرد ریخته می شود. فرایند قالب دائمی تولید قطعاتی با اندازه دانه ریز، استحکام خوب، سطوح صاف و ابعاد دقیق می نمایند. یک پیستون از آلیاژ آلومینیم ریخته شده در قالب دائمی با سطوح تمام شده در شکل (۸-۵) نشان داده شده است.
قطعات ریخته گری قالب دائمی عموماً دارای انقباض و تخلخل گازی کمتر از قطعات قالب ماسه ای و تزریقی ( تحت فشار) است. روش قالب ماسه ای بیشتر برای تولید اقتصادی مقدار کم قطعات بکار می رود، در حالیکه روش قالب دائمی برای ساختن مقدار زیادی قطعات مشابه مورد استفاده قرار می گیرد. در شکل (۹-۵) تعدادی دستگاه قالب گیری دائمی نشان داده شده است. چون قالب دائمی بارها مورد استفاده قرار می گیرد بنابراین مخارج (به ازای هر قطعه) ساخت قالب با افزایش تعداد قطعات تولیدی کاهش می یابد.بطور کلی ریختگی در قالب دائمی یک فرایند با کیفیت خوب است.
افزایش استحکام مکانیکی قطعات ریختگی در قالب دائمی در مقایسه با قطعات ریخته شده در قالب ماسه ای به سرعت بیشتر انجماد درقطعات ریخته شده در قالب دائمی ربط داده می شود. این افزایش سرعت انجماد منجر به تولید دانه ها و اجزاء ساختمانی ریزتر می گردد. برای هر روش ریخته گری یکسری آلیاژهای خاصی مناسبتر از سایر آلیاژها است .برای ریخته گری در قالب دائمی از استفاده از آلیاژهائی که امکان شکست داغ در آنها زیاد است و یا محدوده انجماد گسترده دارند باید اجتناب گردد. به طور کلی آلیاژهای مورد استفاده در فرایند قالب دائمی باید سیالتر از آلیاژهای مورد استفاده در قالب ماسه ای باشد.
۱-طراحی قالب
قالبهای دائمی را قبل از استفاده باید با یک ماده نسوز پوشش داد طوری که قالب فلزی از مذاب آلومینیم محفوظ بماند. با تغییر ضخامت لایه پوششی می توان از آن برای کنتر ل سرعت انجماد نیز استفاده نمود، چون مناطق با نازکترین پوسته پوششی ابتدا منجمد می گردد بنابراین در سطوح مقاطع نازک در راهگاه و تغذیه از پوشش ضخیم تر استفاده می شود.
در قالبهای ماسه ای معمولاً طویل ترین بعد قطعه در امتداد افقی قرار می گیرد. بر عکس در قالبهای دائمی عموماً طولانی ترین بعد در امتداد قائم قرار داده می شود. دو ققطعه ریخته شده در قالب دائمی با راهگاهها و تغذیه های آنها در شکل (۱۰-۵) نشان داده شده است. یک قطعه پیچیده تر، قالب سه قطعه ای آن در شکل(۱۱-۵) دیده می شود.
چون تغییر قالبهای دائمی گران تمام می شود بنابراین بهتر است در طراحی سیستم های راهگاهی و تغذیه گذاری دقت بیشتری مبذول شود. در موارد تردید ابتدا سیستم های کوچکتر از اندازه لازم استفاده شود که می توان به تدریج آنها را بزرگتر کرد تا یک قطعه با کیفیت خوب ساخته شود. قالب دائمی معمولاً از دو نیمه تشکیل شده است که پس از بستن بهم فضای قالب را تشکیل می دهند.
. اگر ماهیچه ای ماسه ای مورد استفاده قرار گیرد. روش عمل را ریخته گری قالب نیمه دائمی می نامند. در هر حال عموماً ماهیچه ها فلز ساخته می شود.
طرح قالب داری باید تا حد امکان ساده باشد. طرح راهگاهی آن باید طوری باشد که محبوس شدن اکسید و گاز در مذاب را به حداقل رسانیده و با انجماد مناسب بخوبی تغذیه گردد. ضخامت مقطع تا حد امکان یکنواخت باشد و مقاطع سبکتر بطور یکنواخت و بدون زاویه تیز به مقاطع سنگین تر وصل شود.
ریخته گری تحت فشار
در ریخته گری تزریقی تحت فشار از طریق وارد کردن آلومینیم مذاب تحت فشار بداخل یک قالب فلزی قطعه ریختگی آلومینیم تولید می گردد. قطعات تولید شده از طریق روش تزریقی فشاری دارای دقت ابعادی خوب، خواص مکانیکی مناسب، سطوح صاف و جزئیات سطحی عالی است. قطعات اگر به تعداد کافی ساخته شوند را می توان با سرعت زیاد و مخارج کم تولید نمود. ماشینکاری زیادی بر روی قطعه ریخته شده مورد نیاز نبوده و می توان تعداد زیادی قطعه تولید نمود در حالیکه سایش قالب بالا نیست، این روش بعلت خارج کم کار برای تولید هر قطعه اهمیت روزافزون می یابد. در بسیاری موارد قطعه ریختگی دارای مقاطع نسبتاً نازکی است. یک نمونه از یک قطعه ریختگی پیچیده که با این روش تهیه شده است در شکل (۱۲-۵) نشان داده شده است، در حالیکه شکل (۱۳-۵) یک دستگاه ریخته گری تحت فشار که قادر به تولید قطعاتی به وزن بیش از ۳۰ کیلو(۷۰ پوند) می باشد را نشان می دهد.
وقتی که فلز مذاب تحت فشار به داخل قالب تزریقی تزریق گردد نیمه های قالب باید کاملاً بهم محکم متصل و بست شده و بهمان حالت باقی بماند. ترتیب انجام کار عبارتست از (۱) بستن قالب، (۲) تزریق فلز تحت فشار؛ (۳)باز کردن قالب و (۴) خارج کردن قطعه.
قطعات ریخته شده را می توان با دست و یا با گیره های اتوماتیک خارج نمود.
اختلاف اصلی بین انواع مختلف دستگاههای ریخته گری تزریقی طریقه وارد کردن مذاب بداخل آنهاست. در مورد ریختگی های آلومینیم بعلت اینکه آلومینیم مذاب به آسانی بر روی فولاد تأثیر می کند از دستگاه تزریقی نوع محفظه سرد استفاده می شود. روش محفظه داغ بندرت برای تولید قطعات ریختگی تزریقی آلومینیم استفاده می شود.
در روش محفظه سرد آلومینیم را با پاتیل بداخل یک محفظه استوانه ای ریخته و سپس بوسیله یک سمبه هیدرولیکی آلومینیم را بداخل قالب تحت فشاری (۳۰۰۰-۲۰۰۰۰ PS۱) ۰/۲-۱۴Kg /mm۲ وارد می کنند. طرز عمل در شکل (۱۴-۵) نشان داده شده است. چون آلومینیم بحالت خمیری می باشد، به این جهت قسمت اعظم گازها قبلاً از فلز خارج شده است. برای ساختن قالب های تزریقی تحت فشار از فولادهای آلیاژی عملیات حرارتی شده استفاده می شود.
قالب گیری پوسته ای
قالب گیری پوسته ای تولید قطعاتی با دقت ابعادی بهتر از قطعات تولیدی در قالب ماسه ای ترمی نماید، ولی کم دقت تر از ریخته گری تحت فشار است. فرآیند قالب گیری پوسته ای را می توان مکانیزه نموده و بخوبی برای تولید تعداد کم قطعات آلومینیمی که نیاز به دقت ابعادی و سطح تمام شده خوب دارد بکار برد.
طریقه ساخت ماهیچه های پوسته ای که قبلاً در این فصل ذکر گردید بهمان طریقه ساخت قالبهای پوسته ای می باشد، فرآیند تولید قالب های پوسته ای بطریق ترسیمی در شکل (۱۵-۵) نشان داده شده است، که شامل مراحل زیر است:
مرحله ۱-ماسه ریز سیلیسی (۲۰۰-۱۵۰ AFS) و یک پودر زرین فنولیک در یک مخلوط کن مخلوط شده و به یک جعبه منتقل می گردد.
مرحله ۲-یک مدل اولیه فلزی بمدت ۱۰ تا ۲۰ ثانیه در (۵۰۰-۴۰۰ درجه فارنهایت) ۲۶۰-۴۰۴ درجه سانتی گراد حرارت داده می شود و سپس با یک محلول سیلیکونی پاشش شده و در جعبه فوق قرار می گیرد.
مرحله ۳-جعبه همراه با مدل جعبه ای معکوس شده و اجازه می دهد که مخلوط رزین-ماسه نزدیک فلز داغ در هم رفته و تشکیل یک پوسته را دهند.
مرحله۴-سپس جعبه بحالت اول درآمده و مدل صفحه ای همراه با پوسته مساه رزین برداشته می شود.
مرحله ۵-صفحه مدلی و پوسته ماسه-رزین و در یک آون در ( ۷۵۰-۶۵۰ درجه فارنهایت) ۳۹۹-۳۴۳ درجه سانتی گراد بمدت ۶۰-۳۵ ثانیه پخته می شود.
مرحله ۶-قالب پوسته ای سخت شده از مدل صفحه ای برداشته می شود.
مرحله ۷-همین روش در مورد نیمه دوم قالب نیز انجام می گیرد.
مرحله ۸-دو نیمه قالب بهم بست شده و در بعضی موارد د ر پشت و اطراف آن ماسه یا فلز به عنوان پشتیبان قرار می گیرد.
سپس فلز بداخل قالب ریخته می شود. پس از انجماد، قطعه تمام شده را با ضربه از قالب خارج می کنند.
روش های دیگر ریخته گری
۱-ریخته گری در قالب گچی
ریخته گری در قالب گچی یک روش تخصصی است که برای تولید قطعاتی با سطوح صاف، دقت ابعادی زیاد و سختی یکنواخت مورد استفاده قرار می گیرد. این روش اصولاً مثل روش ریخته گری در ماسه است، با این تفاوت که به جای ماسه از گچ استفاده می گردد، طبیعتاً قالب گچی گران بوده و باید پس از هرقالب گیری آن را با شکستن قالب خارج نمود.
قالب گچی را می توان برای ساختن طرحهای جدید قطعات بصورت آزمایشی و بدون اینکه قالب های گران قیمت مورد استفاده قرار گیرد بکار برد. عموماً قطعات کوچک (کمتر از یک کیلوگرم) بوده و قالب با گچ ژیپس ساخته می شود. در مورد خشک کردن کامل قالب گچی قبل از استفاده از آن باید دقت لازم صورت گیرد. انتخاب آلیاژ آلومینیم نیز مهم است. آلیاژهای Al- Si بعلت سیالیت های آنها بهترین انتخاب برای ریخته گری قالبهای گچی است.
۲-ریخته گری گریز از مرکز
ریخته گری گریز از مرکز از طریق ریختن مقدار معینی فلز بداخل یک قالب که در حال دوران حول محور خود بوده و یا پس از ریختن بدوران درمی آید انجام می گیرد. عمل گریز از مرکز که تا انجماد فلز ادامه دارد باعث می شود که فلز به طرف دیواره قالب به مکانهائی که در دورترین فاصله از محور دورانی است منتقل گردد. قطعات ریخته شده بطریق گریز از مرکز دارای ساختمان یکنواخت تر و خواص مکانیکی بالاتر از قطعات ریخته شده بطریق دیگر است. اغلب آلیاژهای آلومینیم را می توان بطریق گریز از مرکز ریخته گری کرد ولی آلیاژهای با محدوده انجماد باریک ترجیح داده می شود.
۳-ریخته گری دقیق-قالبهای سرامیکی
این روش ریخته گری آلومینیمی با خواص مکانیکی و فیزیکی مشابه با قطعات ریخته گری در ماسه ولی با دقت ابعاد مشابه قطعات ریخته گری تزریقی می نماید. در فرآیند ریخته گری دقیق(یا ریخته گری با مدلهای مومی) یکنوع گچ نسوز در اطراف یک مدل مومی کار گذاشته می شود. وقتی که گچ گرفت قالب در یک آون خشک شده و مدل مومی ذوب شده و خارج می شود. قالبهای ریختگی دقیق مانند قالبهای گچی را فقط یکبار می توان استفاده کرد زیرا برای خارج کردن قطعه باید آن را شکست.
فرآیند ریخته گری دقیق روش گرانی است زیرا از چندین مرحله تشکیل شده است. چون سرعت انجماد در این روش نسبتاً آهسته است به این جهت نسبت به ریخته گری قالب دائمی یا تحت فشار دانه ها و اجزاء میکروسکوپی درشت تری تولید می شود. در هر حال به علت دقت روش قالب دقیق، از این روش برای ساختن قطعات پیچیده که تولید آنها بطریق دیگر ریخته گری و یا ماشینکاری اقتصادی نیست استفاده می شود.
مقایسه روشهای مختلف ریخته گری
هر یک از روشهای ریخته گری آلیاژهای آلومینیمی دارای مزیت و معایب مخصوص خود می باشد. جدول ۳-۵ فاکتورهای موثر مهم در انتخاب روشهای ریخته گری در ماسه، قالب دائمی، تزریقی یا در گچ برای ساختن قطعات آلومینیمی را نشان می دهد. ترکیب این روشهای ریخته گری روز بروز اهمیت بیشتری می یاابد. برای مثال برای آهسته کردن انجماد می توان از گچ در یک قسمت قالب و برای سرعت دادن انجماد از فولاد در قسمت دیگر استفاده شود.
در یکی از فصول دیگر در مورد انتخاب و خواص آلیاژهای ریختگی برای هر کدام از این روشها بحث خواهد شد. فصول دیگر نیز به عملیات حرارتی، جوش و اتصال، مقاومت خوردگی و عملیات سطحی آلیاژهای آلومینیمی ریختگی و کارپذیر خواهد پرداخت.
منبع: وبلاگ آقای ذهبی نیا