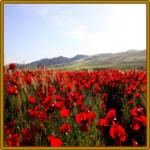
سلام به وب من خوش آمدید دوستان و همراهان عزیز از اینکه مهمان این وب هستید بسیار سپاسگزارم منتظر نظرات سازنده ی شما دوستان هستم
عنوان | پاسخ | بازدید | توسط |
![]() |
1 | 1216 | piskesvat |
![]() |
3 | 2710 | mehran99 |

مقدمه :
اخیراً محققان از مدل یخی جهت ساخت قالب سرامیکی برای ریخته گری دقیق استفاده به عمل آورده اند. در این روش به دلیل مشخصه های ویژه یخ، مخلوط قالب سرامیکی بایستی به گونه ای باشد متفاوت از قالب های پوسته ای مورد استفاده در ریخته گری دقیق با مدل های بومی می باشد که در دمای محیط و بالاتر به خودگیری لازم می رسند. مهمترین عاملی که در ریخته گری با مدل یخی بایستی کنترل گردد چقرمگی شکست قالب سرامیکی می باشد که در واقع مقاومت و استحکام آن را در مراحل بعدی ذوب ریزی نشان می دهد. مخلوط قالب گیری در این روش عموماً حاوی سیلیکای گداخته، پودر سیلیکات آلومینیوم، رزین و کاتالیزور می باشد که در مراحل بعدی بیشتر توضیح داده خواهند شد. در این مقاله با تغییر دادن نسبت وزنی سیلیکای گداخته فیبر دار به پودر سیلیکات آلومینیوم و نیز مقادیر رزین و کاتالیست، مقدار چقرمگی شکست اندازه گیری و سطح مقطع شکست نمونه ها برای بررسی مکانیزم شکست مورد بحث و بررسی قرار گرفته است. نتایج نشان می دهد افزایش سیلیکای گداخته فیبردار باعث افزایش چقرمگی شکست نمونه و مقاومت در برابر ترک ناشی از ذوبریزی می گردد. در این میان میزان رزین مصرفیط و کاتالیست نیز روی نسبت بهینه مورد اشاره تأثیر مستقیم می گذارد.
خلاصه:
موم معمول ترین ماده مورد استفاده در ساخت مدل برای ریخته گری دقیق می باشد. تنش های اعمالی از طرف موم در حین ذوب برای تخلیه شدن باعث بروز مشکلات عمده ای شامل بروز ترک در پوسته می گردد [1]. مطابق آنچه که ریچارد و ساندرلند [2] نشان داده اند، موم تا حدی مشابه پلیمر های خطی بلوری می باشد که در اثر ذوب شدن، یک افزایش ناگهانی در حجم آن رخ می دهد. این افزایش حجم عامل اصلی بروز ترک در قالب پوسته ای در مرحله پخت به شمار می رود. در شکل 1 مقایسه ای پوسته تولید شده با مدل های یخی و مومی نشان داده شده است.
همانطور که در شکل 1 ملاحظه می گردد تمایل به بروز ترک در پوسته تولیدی از مدل مومی بالا می باشد و این در حالی است که میزان ترک در پوسته حاصل از مدل یخی در حد صفر می باشد.
فرایند ریخته گری با مدل یخی [1] (FCP ) یکی دیگر از روش های ریخته گری دقیق به شمار می رود که توسط Yodice [3] اختراع گردیده است. در این فرایند که اساس آن مشابه ریخته گری دقیق با مدل مومی می باشد از یخ در ساخت مدل برای ریخته گری قطعات فلزی استفاده به عمل می آید. Yodice و سایر همکارانش امکان پذیری این روش را کاملاً به اثبات رساندند [6- 4]. مزیت عمده روش ریخته گری با مدل یخی برای جایگزین کردن با روش قدیمی مدل مومی می تواند مقرون به صرفه بودن، سهولت فرایند و کیفیت سطحی بسیار بالا در تولید قطعات نزدیک به شکل نهایی باشد. برای تولید مدل های سه بعدی و پیچیده یخی عموماً از روش نمونه سازی با انجماد سریع استفاده می کنند. در این روش مدل یخی را مستقیماً از روی مدل طراحی شده کامپیوتری و با انجماد لایه به لایه قطره های آب می سازند [10- 7].
در این روش با توجه به ذوب شدن یخ در دمای محیط فرایند قالبگیری می بایستی در دمای زیر صفر صورت گیرد. در نتیجه مواد قالبگیری در این روش بایستی مشخصه های ویژه ای داشته باشند و این نیاز به مطالعات وسیعی برای یافتن موادی که در دمای زیر صفر به خودگیری لازم برسند، دارد. امروزه اگر چه این روش به خوبی قابل اجرا می باشد ولی تعداد منابع علمی و تدوین شده در این رابطه وجود دارد. بررسی ها نشان می دهد موفقیت در انجام روش FCP شدیداً وابسته به چقرمگی قالب ساخته شده می باشد. لذا مطالعات روی این پارامتر همراه با بررسی سطوح شکست اساس این تحقیق را تشکیل می دهد. عوامل اصلی که در این تحقیق مورد بررسی قرار گرفته است شامل نسبت وزنی سیلیکای گداخته [2] (FS ) حاوی فیبر به ماده نسوز سیلیکات آلومینیوم و مقدار حجمی رزین و کاتالیست مورد استفاده در تهیه مخلوط قالب گیری می باشد. همچنین برای تبیین مکانیزم شکست در قالب های پوسته ای سطح شکست و ریزساختار نمونه های آزمایشی با میکروسکوپ الکترونی تحت بررسی قرار گرفته شد. مدل انتخابی در این تحقیق پیچ M8 می باشد تا از نقاط تیز و پیچیدگی لازم برخوردار باشد.
انتخاب مواد مناسب برای قالبگیری در دمای زیر صفر :
موادی که برای ساخت قالب در ریخته گیری دقیق با مدل یخی مورد استفاده قرار می گیرد بایستی مشخصه های ویژه و متفاوت با آنچه در مدل مومی مورد نیاز بوده را داشته باشد [15- 11]. برای مثال چسب مورد استفاده در روش FCP
بایستی عاری از آب باشد تا در دمای زیر صفر منجمد نگردد. حال در این قسمت مخلوط قالب گیری برای تولید پوسته سرامیکی را توضیح خواهیم داد.
مخلوط سرامیکی :
همانند دیگر روش های ریخته گری دقیق دوغاب مورد استفاده برای پوشش دهی مدل یخی مخلوطی از چسب و مواد نسوز سرامیکی می باشد. لذا این مواد نقش حیاتی را در ساخت پوسته ایفا می کنند. دامنه تغییرات مواد نسوز مورد استفاده بسیار وسیع می باشد و معمولاً ترکیبی از ماسه سیلیسی، سیلیکات آلومینیوم، آلومین، سیلیکای گداخته (FS ) و سیلیکات زیر کنیم می باشد. انتخاب مواد نسوز مناسب در حصول قطعه ای با کیفیت سطحی، دقت ابعادی و خواص بالا امری ضروری می باشد.
در انتخاب مواد قالب گیری موارد زیر بایستی مد نظر قرار گیرد : درجه دیرگذاری، ضریب انبساط حرارتی، ترکیب شیمیایی، مسایل هزینه ای، اندازه و توزیع دانه بندی مواد نسوز.
همانند ماسه ماهیچه و قالب گیری دانه بندی ذرات مواد نسوز و نیز نسبت آنها در ترکیب مواد قالب گیری روی کیفیت نهایی پوسته و قطعه حاصله مستقیما اثر می گذار می باشد. در این تحقیق از سیلیکات آلومینیوم به عنوان ماده نسوز قالب گیری استفاده به عمل آمد. ولی همانطور که در شکل a 2 نشان داده شده است استحکام حاصله در پوسته پایین بوده و باعث ایجاد ترک در آن شده است. برای بهبود آن از وجود سیلیکای گداخته فیبردار در ترکیب مواد قالب گیری استفاده به عمل آمد و همانطور که در شکل b 2 نیز نشان داده شده است باعث بهبود استحکام در قالب پوسته ای شده است.
چسب :
جزء اصلی دیگر در مخلوط قالب گیری چسب می باشد که در اثر ترکیب با مواد نسوز تشکیل دوغاب را می دهد. برای ریخته گری دقیق در دمای پایین حلال مورد استفاده در چسب نبایستی منجمد گردد و در دمای زیر صفر نیز از سیالیت لازم برخوردار بوده باشد. در کنار این مشخصه ها لازم است قالب حاصل از آن استحکام بالایی داشته و باعث حصول قطعه ای با کیفیت سطحی و دقت ابعادی عالی گردد. بر اساس معیار های اشاره شده در این تحقیق سه نوع چسب مورد آزمایش قرار گرفت : آب شیشه، سیلیکای ژله ای و سیلیکات اتیل. قالب ساخته شده با چسب سیلیکات سدیم (آب شیشه ای) دارای استحکام گرم پایینی بود و علاوه بر آن دقت ابعادی و کیفیت سطحی قطعات تولیدی نیز پائین می بود. به همین دلیل در آزمایشات بعدی از آب شیشه استفاده نگردید. چسب دوم سیلیکای ژله ای بودکه از ترقیق کردن آب شیشه به میزان 10- 9 برابر با افزودن آب بدست می آید. لذا با توجه به این که 50- 40 درصد وزنی آن را آب تشکیل می دهد در دمای زیر صفر سریعاً منجمد گردیده و لذا امکان استفاده از سیلیکای ژله ای نیز مقدور نگردید. در مرحله بعدی آزمایشات که از سیلیکات اتیل استفاده به عمل آمد تمامی خواص مورد نیاز حاصل گردید.
کاتالیست :
جهت کوتاه کردن مدت زمان ژله ای شدن و خودگیری دوغاب (مخلوط چسب با مواد نسوز سرامیکی) جهت ساخت قالب برای ریخته گری دقیق در دمای پائین نیاز به استفاده از یک کاتالیزور می باشد. به عبارتی دیگر بدون استفاده از کاتالیزور ممکن است زمان ژله ای شدن روز ها به طول انجامد. مدت زمان ژله ای شدن به عواملی چون دما، ترکیب چسب مصرفی و PH دوغاب بستگی دارد. اثر PH در این رابطه برجسته تر از دو عامل دیگر می باشد. زمانی که عدد PH برابر با 2 باشد پایداری دوغاب افزایش یافته و در نتیجه مدت زمان ژله ای شدن افزایش می یابد. زمانی که 6- 5 = PH باشد دوغاب بسیار ناپایدار شده و در نتیجه زمان ژله ای شدن کوتاهتر می گردد. زمانی که 1 < PH باشد نیز شرایط مشابهی پیش می آید. لذا کاتالیزور مورد استفاده بایستی PH دوغاب را از دامنه پایدار به ناپایدار تغییر دهد.
لذا با توجه به استدلال بالا کاتالیزور مورد استفاده یا بایستی خاصیت اسیدی داشته باشد که عدد PH را به زیر یک برساند و یا اینکه خاصیت قلیایی داشته باشد تا عدد PH را به دامنه 7- 6 برساند. در این میان از جمله مهمترین کاتالیست های اسیدی می توان به اسید سولفوریک، کلریک و فسفریک اشاره نمود و از جمله مهم ترین کاتالیست های بازی نیز می توان به Na(OH), MgO , Ca(OH)2 Mg(OH)2 , Na2CO3 اشاره نمود. با توجه به نتایج آزمایشات انجام پذیرفته در مرجع [6] استفاده از کاتالیزور های آلی باعث تشکیل دوغاب و در نتیجه قالب پوسته ای با کیفیت و خواص بالا و قطعه با کیفیت و خواص بالا و قطعه با کیفیت سطحی عالی می گردد. در مقابل کاتالیزور های اسیدی در مرحله پخت به سطح داخلی پوسته رفته و باعث افت شدید خواص مکانیکی در دمای بالا می گردد. همچنین بقایای کاتالیست های غیرآلی باعث خروج فاز های پیوندی از حالت شیشه ای و در نتیجه بروز ترک در قالب می گردد. این در حالی است که کاتالیست های آلی در مرحله پخت کاملا سوخته و از سیستم خارج شده و لذا خواص گرم پوسته را تحت تاثیر قرار نمی دهد.
مخلوط دوغاب :
این مخلوط شامل پودر سرامیکی، چسب و کاتالیست می باشد. درصد وزنی هر کدام از این اجزاء روی عملکرد دوغاب، کیفیت و خواص قالب پوسته ای و در نهایت کیفیت قطعه نقش مهمی را ایفا می نماید. بر این اساس مواد زیر برای انجام آزمایشات انتخاب گردیدند :
مخلوطی از سیلیکات آلومینیوم و سیلیکای گداخته فیبردار به عنوان پودر سرامیکی و سیلیکات اتیل اتیل هیدرولیز شده به عنوان چسب و مخلوطی از اتانول با تری اتانول آمین (با نسبت 1 : 5/ 1) به عنوان کاتالیست.
دانه بندی و توزیع ذرات سیلیکای گداخته و سیلیکات آلومینیوم در جداول 2 و 1 آورده شده است.
جهت اطمینان از تکرارپذیری نتایج آزمایشات اقدامات احتیاطی زیر انجام پذیرفت :
· نگهداری چسب در داخل شیشه های ایزوله و قراردهی آن در یخچال جهت رسیدن به دمای محیط کاری (15- درجه سانتیگراد)
· نگهداری پودر های سرامیکی در ظروف شیشه ای ایزوله و قراردهی آن در یخچال جهت رسیدن به دمای محیط کاری.
حرارت دادن آنها به مدت 2 ساعت در 240 درجه سانتی گراد جهت کنترل رطوبت قبل از استفاده
· اختلاط تری اتانول امین و اتانول با نسبت های ذکر شده و نگهداری آن در شیشه های ایزوله و قرار دهی آن در یخچال جهت رسیدن به دمای محیط کاری.
· اندازه گیری دقیق وزنی هر کدام از مواد در هر آزمایش
روش انجام آزمایش :
متغیر های فرایند :
متغیر های این فرایند بدین شرح انتخاب گردید : مقدار کاتالیست، مقدار چسب و نسبت سیلیکای گداخته به سیلیکات آلومینیوم. همانطور که در جدول 3 نیز نشان داده شده است برای هر کدام از این متغیر ها نیز سه داده در نظر گرفته شد.
لذا همانطور که در جدول 4 نشان داده شده تحقیق حاضر شامل 9 آزمایش خواهد بود. لازم به ذکر است زمان اختلاط با توجه به تجربیات قبلی نویسنده روی 4 دقیقه ثابت و دمای کاری در تمامی آزمایشات 15-درجه سانتیگراد در نظر گرفته شد.
آماده سازی نمونه ها :
نمونه های آزمایش مورد استفاده در این آزمایش به روش ریخته گری دوغاب تهیه گردید. بدین شکل که دوغاب آماده شده به شرح زیر در داخل قالب یخی ریخته شده و سپس با ذوب کردن یخ نمونه های بدست آمدند.
1. پودر های از پیش خشک شده به محض خروج از فریزر وزن شده و در داخل مخزن میکسر تحت خلا ریخته می شود.
2. چسب توسط ترازوی از پیش سرد شده توزین شده و در داخل مخزن میکسر تحت خلا ریخته می شود.
3. کاتالیست از پیش مخلوط شده به داخل مخزن میکسر تحت خلا ریخته می شود.
4. سرپوش مخزن میکسر گذاشته می شود و عملیات اختلاط تحت شرایط خلا صورت می پذیرد.
5. بلافاصله پس از اتمام اختلاط دوغاب حاصله در داخل قالب یخی ریخته می شود.
لازم به ذکر است پس از اتمام اختلاط و قبل از بارریزی دمای مخلوط به 4- درجه سانتیگراد رسیده بود.
در شکل 3 ابعاد و شکل هندسی نمونه های آزمایشی ریخته شده در قالب یخی بر اساس استاندارد ASTM C1161-02c نشان داده شده است.
پس از پخت و درآوردن نمونه ها ابعاد آنها توسط دستگاه های دقیق اندازه شد و سپس جهت تست خمشی با دستگاه دارای چهار تکیه گاه آماده گردید. در شکل 4 نمای شماتیک دستگاه تست خمش همراه با توزیع تنش در آن نشان داده شده است.
در رابطه با دستگاه تست خمش :
تست خمش با مشخصات ذکر شده برای دستگاه آن سال هاست که روش قابل اعتمادی برای اندازه گیری استحکام خمشی به شمار می رود.
که در این رابطه S استحکام خمشی، P نیروی اعمالی برای شکست، L فاصله بین دو تکیه گاه بیرونی، b عرض و d ضخامت نمونه آزمایشی می باشد که در شکل 3 و 4 نشان داده شده است. برای محاسبه چقرمگی شکست سطح زیر منحنی توزیع تنش محاسبه می گردد که نمونه ای از آن در شکل 4 نشان داده شده است. لازم به ذکر است نرخ بارگذاری توسط دستگاه psi/min 10 می بود و برای هر کدام از آزمایشات طراحی شده در جدول 4 به تعداد 20 عدد نمونه آزمایش گردید و در مجموع 180 عدد نمونه ریخته شد.
فرآیند تولید قطعه در FCP :
فرایند تولید قطعه در روش ریخته گری دقیق با مدل یخی تا حد زیادی مشابه همین روش با مدل مومی بوده و شامل مراحل زیر می باشد :
· ساخت مدل یخی با استفاده از قالب سیلیکونی و یا روش نمونه سازی سریع انجمادی
· تولید سیستم راهگاهی از یخ به روش مشابه و مونتاژ آنها به مدل مربوطه
· پوشش دهی مجموعه مونتاژ شده با یک ماده جداکننده [14- 11]
· دوغاب دهی مجموعه حاصله با دوغاب سرامیکی از قبل آماده شده
· انتقال مجموعه دوغاب دهی شده پس از ژله ای شدن در دمای محیط جهت ذوب شدن یخ
· حرارت دهی در دمای 900 درجه سانتیگراد به مدت زمان معین برای شکل گیری قالب پوسته ای
· ریختن مذاب با شرایط معین در داخل پوسته سرامیکی
· در آوردن قطعه ریختگی و عملیات تمیزکاری بعدی
بحث و نتیجه گیری :
نتایج استحکام خمشی حاصل از تست شکست نمونه های سرامیکی نشان گر وجود پراکندگی قابل ملاحظه داده ها می باشد. جهت برآوردن میزان قابلیت اطمینان به نتایج حاصله نیاز به یک سری ابزار های آماری جهت تعیین و مقایسه تغییر پذیری می باشد. برای این منظور مدول Weibull در این تحقیق مورد استفاده قرار گرفت که مجال پرداختی به این موضوع در این مقاله میسر نمی باشد. لازم به ذکر است در جدول 4 این مشخصه برای هر کدام از آزمایشات تعیین گردیده است.
نتایج بدست آمده از این تحقیق نشان گر این موضوع می باشد که با افزایش مقدار سیلیکای گداخته فیبردار چقرمگی شکست پوسته سرامیکی زمانی افزایش می یابد که مقدار سیلیکای گداخته افزوده شده از حد معینی بیشتر باشد. همچنین با کاهش میزان چسب مصرفی چقرمگی شکست افزایش می یابد. بررسی های انجام پذیرفته با میکروسکوپ الکترونی روی سطوح شکست نشانگر این موضوع می باشد که افزودن سیلیکای گداخته فیبردار باعث ایجاد یکپارچگی ساختاری و ممانعت از بروز ترک در آن می گردد.
دقت ابعادی و کیفیت سطحی بالای نمونه های ریخته شده نشانگر این موضوع می باشد که ریخته گری دقیق با مدل یخی برای تولید قطعات با پیچیدگی هندسی بالا بسیار مناسب می باشد.
منبع: ریخته گران اهواز