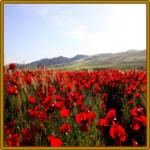
سلام به وب من خوش آمدید دوستان و همراهان عزیز از اینکه مهمان این وب هستید بسیار سپاسگزارم منتظر نظرات سازنده ی شما دوستان هستم
عنوان | پاسخ | بازدید | توسط |
![]() |
1 | 1216 | piskesvat |
![]() |
3 | 2710 | mehran99 |

قالب های بزرگ پرس کاری قطعات خودرو که از طریق ریخته گری ساخته می شوند ، در مقایسه با قالب های ساخته شده به روش آهنگری و فورج ، دارای مزایای متعددی از قبیل تنوع ابعادی ، حجم کم ماشین کاری و همگنی ریز ساختار آلیاژ می باشند. نکته مهم در استفاده از این آلیاژ ، طراحی و نحوه اجرای پروسه ریخته گری است. امروز برای کسب نیازمندی های متنوع شرکت های قالب سازی بزرگ آلمان ، انواع فولادهای کم آلیاژ مخصوص نیز مورد استفاده قرار می گیرند .
قالب ها تأثیر بسیار مهمی در اقتصادی بودن فرآیندهای تغییر شکل فلزات دارند . بر این اساس طی سال های اخیر هزینه های ساخت قالب های بزرگ بیش از بیش مورد توجه قرار گرفته است . در این خصوص ، صرفاً در نظر داشتن هزینه های ساخت آن چنان دقیق نیست ، بلکه کسر تیراژ تولید ، قالب ، هزینه های قالب برای ما اهمیت خواهد داشت . در بخش هزینه های قالب می توان به دوام آن و تناوب اجرای تعمیرات باسازی اشاره کرد . با در نظر داشتن آن چه از قالب های فوق انتظار می رود می بایست بر همین پایه به یک ارزیابی دقیق از میزان تأثیر عوامل دخیل در هزینه های قالب دست یافت تا امکان مقایسه دستاوردهای هر عامل فراهم گردد. بدون شک هزینه مواد قالب نیز در قیمت تمام شده در نظر گرفته می شود . انتخاب این مواد و نحوه عملیات بر روی آن به میزان قابل توجهی بر کسری که قبلاً از آن نام بردیم یعنی کسر تیراژ تولید ، هزینه قالب ، تأثیر خواهد داشت . از طریق ارزیابی دقیق و همه جانبه میزان تاثیر و اهمیت کلیه پارامترهای مؤثر می توان کارآیی یک قالب خاص را به میزان زیادی ارتقاء بخشید .
هزینه مواد اولیه در مقایسه با کل قیمت تمام شده قالب ، بسیار کمتر است . این هزینه علی رغم وجود برخی نظرهای مخالف در این خصوص ، همانند نوک کوه یخی می باشد که از آب سر برآورده و در مقایسه با حجم زیر آب ، درصد بسیار کمی را نشان می دهد .
مقایسه آلیاژهای تولید شده به روش ریخته گری با فولادهای ابزاری آهنگری شده :
از سالها قبل فولادهای ابزاری ریخته گری در قالب های بزرگ صنعتی به شیوه موفقیت آمیزی مورد استفاده قرارگرفته است . در بسیاری از مواقع امکان ساخت چنین قالب هایی با این ابعاد ، از فولاد خشکه ابزاری که قبلا عملیات فورج کاری روی آن انجام گرفته است ، وجود ندارد . علاوه بر این به کارگیری این نوع فولادها مسائل ماشین کاری خاص خود را دارد که همین باعث افزایش هزینه می گردد . از سوی دیگر حجم ماشین کاری در این نوع فولادها به شکل اجتناب ناپذیری زیاد است و این امر باعث دورریز برخی مناطق مستعدتر در ریز ساختار آلیاژ حین ماشین کاری می شود .
فولادهای پر آلیاژی نظیر 1.2379 به دلیل وجود درصد کاربید بالا ، دارای شبکه کاربیدی کاملا بارزی می باشند . به ویژه در فولادهایی با ابعاد بزرگ هر چه به مغز مقطع نزدیک تر می شویم کاربیدها درشت تر و ابعاد شبکه کاربیدی بزرگتر می شود . دلیل این وضعیت هم عدم امکان وجود تغییر شکل های یکنواخت بر تمامی سطح مقطع فولاد می باشد . این حالت بدین معناست که محدوده خارجی مقاطع فورج شده ، تغییر شکل های شدیدتری در مقایسه با ناحیه مرکزی مقطع داشته اند . با استفاده از فولادهای آلیاژی ریخته گیری ، ناحیه کاری فولاد ، منحصر به جداره خارجی قالب ریخته گری خواهد بود . معمولاً در این نواحی از فولادهای پرآلیاژ ریخته گری ، شبکه نسبتاً ریزکاربیدی ناشی از سرعت انجماد بالا پس از ریخته گری تشکیل میشود . حتی در نواحی مرکزی قطعات تولیدی به روش ریخته گری در مقایسه با مقاطع فورج شده دارای شبکه نسبتاً ریزتری می باشند و در کل امروزه روش های ریخته گری ساختار همگن تری به دست می دهد .
تکنیک های ریخته گری :
فولادهای آلیاژی مخصوص قالب ، معمولاً از طریق مدل های فرمی ساخته می شوند . طراحی ریخته گری این قطعات با توجه به فرم هندسی قطعه و از نقطه نظر اجرای عملیات ریخته گری انجام می پذیرد . در ریخته گری قطعات فولاد آلیاژی ، این مرحله تا حدی مشکل ساز می باشد . در حالی که انقباض چدن نشکن حدود 2% می باشد ، در نواحی مرکزی قطعه فولاد آلیاژی حدود 12% انقباض حجمی رخ می دهد . برای آن که در نقاط کاری قالب تغذیه کافی صورت گیرد ، آماده سازی قبلی مدل ریخته گری ، با در نظر داشتن ویژگی های انجماد قطعه ضروری است . این آماده سازی باید به نحوی انجام شود که نواحی کاری قالب در قسمت تحتانی قالب ماسه ای قرار گیرد تا حجم انقباض به سمت بالا و به داخل تغذیه هایی که در بخش فوقانی مدل قرار داده شده است هدایت شود .
دیواره های تقویتی در برخی از نقاط ضخیم تر در نظر گرفته می شوند تا سطح مقطع راه گاه افزایش یابد . اولین ناحیه ای که از طریق این تغییرات منجمد می شود ، سطح روی قالب خواهد بود . سپس جبهه انجماد به سمت دیواره های تقویتی پشت سطح رویه قالب حرکت می کند و نهایتاً در داخل تغذیه ها به پایان می رسد . بنابراین از طریق تغذیه های کار گذاشته شده ، می توان هر گونه کسری حجمی ناشی از انجماد را پس از ریخته گری ، با بارریزی مجدد ذوب ، داخل تغذیه ها جبران نمود .
در ریخته گری قالب های بزرگ فولادی تنها با این شرایط می توان به قطعه ای با کمترین تخلخل و حفره انقباضی دست یافت . افزون بر این طی مراحل قالب گیری و ریخته گری برخی مشکلات دیگر می تواند روی دهد . به عنوان مثال استفاده از چسب و یا نوارهای چسب در ساخت مدل ضروری به نظر می رسد ، اما این مواد حین بارریزی ایجاد گاز می کنند و باعث افت کیفیت قالب می شوند . بنابراین می بایست قبل از ساخت مدل ، طرح قالبی که قرار است ریخته گری شود توسط واحد ریخته گری کنترل و باز بینی شود . داده های سطوح قالب از قبل به واحد ریخته گری ارائه می گردد تا در صورت نیاز پس از بررسی ، اصلاحات ضروری بر روی آن انجام شود ، در نهایت به اصلاحات کمتری پس از ساخت مدل نیاز است و تا حد ممکن کاربرد مواد چسبی محدود می شود .
بسته به کاربردهای مختلف ، فولادهای متنوعی در بازار جهت استفاده وجود دارند . تمامی آلیاژها که فولادهای آن به شکل مقاطع فولادی در بازار عرضه می شوند را می توان به شکل آلیاژ ریخته گری جهت قالب ریزی مورد استفاده قرار داد . در حالی که فولادهایی از قبیل 1.2769 و 1.2602 جایگاه خوب و خاص خود را در ریخته گری قالب های بزرگ پرس کاری بدست آورده اند ، در دیگر فولادهای آلیاژی نیز به وضوح قابلیت های جدیدی دیده می شود . از آن جا که ساخت این قالب ها اغلب در واحدهای ذوب کوچکتر انجام می شود ، شرکت هایی که در ریخته گری فولادهای آلیاژی فعالیت دارند، می توانند بنا به نوع آلیاژ مورد نیاز دامنه انتخاب گسترده داشته باشند . از سوی دیگر خواص قطعات ریخته گری شده از طریق اجرای عملیات تکمیلی بعدی مثل عملیات حرارتی یا تغییر شکل ، قابلیت تنظیم و اطلاح دارد .
فولاد شماره 1.7140 و 1.2769 :
این گرید به عنوان فولاد کم آلیاژی بهسازی شده شناخته می شود . بسته به کاربرد آن و پروسه های تولیدی بعدی ، شرایط عملیات حرارتی متفاوتی را می توان بر روی این فولادها اجرا نمود . از یک سو این فولادها در حالت نرمالیزه و آنیل و یا از سوی دیگر در شرایط عملیات حرارتی شده با استحکام های متفاوت به بازار عرضه می شوند . قابلیت کار برروی این فولادها با شرایط آنیل بسیار مناسب خواهد بود . اما اگر کارآیی از فولاد انتظار رود می بایست فولاد عملیات حرارتی شده را مورد استفاده قرار داد . بر روی هر دو نوع این فولاد فولادها می توان عملیات حرارتی سطحی مثل سخت کاری القایی را انجام داد . با این روش مقاومت به سایش در نواحی که خطر این پدیده وجود دارد کاهش می یابد . معمولاً این عملیات سطحی می بایست با خنک کاری طبیعی بدون استفاده از مایعات خنک کننده فولاد تکمیل شود . در این روش حداکثر سختی قابل دستیابی حدود 56 Hrc است .
این نوع فولادهای نسبتاً کم آلیاژ ریخته گری آسان تری را دارند و همچنین قطعات بزرگ که بعدا بتوان آن را عملیات حرارتی بهسازی نمود بدون مشکل خواهد بود .
فولاد شماره 1.2333 و 1.2320gp3m اسم تجارتی
قالبسازان به طور مداوم نیازمندی های جدیدی برای ریخته گری قالب ها تعیین می کنند که با مواد قدیمی تر قابل دسترسی نیست .
- قابلیت ساخت و تولید در ابعاد بسیار بزرگ .
- شکنندگی کمتر ( کم بودن درصد کربن ) .
- امکان تحویل در حالت عملیات حرارتی شده .
- قابلیت سخت کاری سطحی تا 60hrc .
- قابلیت جوش کاری بدون نیاز به عملیات پیش گرم .
فولادی مانند 1.2320 که دارای درصد آلیاژی بیشتر است ، به خوبی از عهده شرایط فوق برآمده است . با توجه به این واقعیت که گرید 1.2333 از نظر وزن قابل ریخته گری دارای محدودیت می باشد ، قطعات ریخته گری می بایست قبلا از نظر طرح هندسی مورد ارزیابی قرار گیرند . کسب سختی پذیری بالاتر این نوع آلیاژ ، بسته به طرح قطعه و تکنیک ریخته گری مورد استفاده قرار می تواند مشکل ساز شود .
عنصر کربن در هر دو آلیاژ حدود 06/.% می باشد . از این رو عملاً دارای فاز کاربیدهای اولیه نبوده و نتیجتاً از قابلیت چکش خواری نسبتاً خوبی برخوردار هستند . به دلیل وجود درصد کربن بیشتر در مقایسه با فولادهای 1.2769 و 1.7140 قابلیت سختی پذیری در مقایسه با گریدهای قبلی را دارند .
بسته به دمای آستینه کردن درجه سختی فولاد می تواند تا حد 63hrc پس از سرد کردن سریع افزایش یابد . بر روی هر دو آلیاژ به روش های متنوعی می توان سخت کاری سطحی را اجرا نمود . حتی قطعات کوچک را می توان به شکل کلاسیک در کوره خلاء تحت عملیات حرارتی قرار داد .
نتایج آزمایش های جوش کاری نشان می دهد که علی رغم وجود فازهای آلیاژی پایدار ، هردو آلیاژ از قابلیت جوش پذیری خوبی برخوردار هستند . هر جند در حین جوش کاری لازم است از طریق چکش کاری ممتد اقدام به حذف تنش های پسماند ناشی از انقباض حرارتی کرد و خطر ایجاد ترک های گرم را به حداقل رساند . با در نظر داشتن نکات کلیدی فوق می توان برروی هر دو آلیاژ فوق بدون عملیات پیش گرم اقدام به جوش کاری نمود . در جوش کاری های عمیق نیز استفاده از یک لایه زیرکار با الکترود آستینی سودمند خواهد بود .
فولاد 1.2370 :
این آلیاژ طی سال های اخیر در ساخت قالب های برش ، کاربرد روزافزونی یافته است . وجود درصد کاربید بالا در ساختار ، این فولاد را از قابلیت برشی مناسب و مقاومت سایشی بالایی بهره مند کرده است . هر چند در مقایسه با فولاد 1.2382 دارای کربن کمتر و قابلیت چکش خواری و جوش پذیری بهتری می باشد ، اما اتخاذ تدابیر خاص جهت جلوگیری از بروز ترک حین جوشکاری در آن آلیاژ اجتناب ناپذیر است .
فولاد 1.2382 :
فولاد سردکار 1.2382 با حدود 15% فاز کاربید در ریز ساختار ، از دیگر آلیاژها متمایز است و درکل خانواده فولادهای ریخته گری مخصوص قالب های پرس کاری ، از بیش ترین مقاومت سایشی و قابلیت برشی برخوردار است . این فولاد پر آلیاژ در مقایسه با فولادهای کم آلیاژتر دارای محدوده گسترده تری از دمای سخت گرانی است و می توان آن را در محدوده دمایی 1020 تا 1080 درجه سانتی گراد بدون خطر رشد بیش از حد دانه های ریز ساختار حرارت داد . بالطبع در این نوع آلیاژها با افزایش دمای آستینه کردن ، حلالیت کربن در شبکه کریستالی بیشتر می شود . و درصد آستنیت باقی مانده بالا می رود . هر چه دمای آستنیته بالاتری مورد استفاده قرار گیرد به ناچار می بایست درصد آستنیت باقی مانده را از طریق برگشت چند مرحله ای در محدوده دمایی بالای 500 درجه سانتی گراد مورد استحاله قرارداد . با این کار می توان به یک ساختار همگن و پایدار دست یافت .