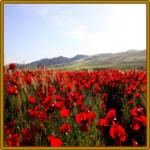
سلام به وب من خوش آمدید دوستان و همراهان عزیز از اینکه مهمان این وب هستید بسیار سپاسگزارم منتظر نظرات سازنده ی شما دوستان هستم
عنوان | پاسخ | بازدید | توسط |
![]() |
1 | 1216 | piskesvat |
![]() |
3 | 2712 | mehran99 |

1- هیدروژن : |
در گذشته براي جلوگيري از تلفات مذاب قلع را در پاتيل تا يك 0.1 % به مذاب اضافه مي شود كه اين مقدار باعث افزايش خواص مكانيكي چدن مي شود اين عنصر داراي نقطه ذوب 450 درجه سانتيگراد بوده و عموما به صورت شمش هاي 15 الي 20 گرمي استفاده مي شود
13- تيتانيم :
اين عنصر مانع از انحلال اكسيژن و نيتروژن درمذاب چدن مي شود همچنين باعث توزيع يكنواخت گرافيت و افزايش خواص مكانيكي در چدن ها مي شود .
14- واناديم :
اين عنصر باعث يكنواختي توزيع گرافيت و همچنين پايداري فاز سمنتيت در چدن ها مي شود اين عنصر باعث افزايش خواص مكانيكي شده و عاملي است كاربيد زا است كه تا حدود 1% به مذاب چدن اضافه مي شود
15- منگنز :
اين عنصر جزو عناصر كاربيد زا بوده و تاثير منفي گوگرد را كاهش مي دهد كه اين واكنش شيميايي به صورت زير نمايش داده مي شود . FeS+Ma=MaS
درجه حرارت ذوب اين فلز 1200 تا 980 درجه سانتيگراد است كه سولفيد منگنز در اين دما به صورت فازي در داخل دانه ها رسوب مي كند اين فاز خواص مكانيكي را افزايش داده و در بعضي مواقع از طريق سرباره خارج مي شود منگنز باعث افزايش مقدار كاربيد شده كه اين امر موجب افزايش سختي و مقاومت به ضربه آلياژ مي شود اين عنصر تا حدود يك درصد به مذاب اضافه مي شود
مرحله دوم : روش هاي گوگرد زدايي :
1- اضافه كردن مواد گوگرد زدا در كف پاتيل و ريختن مذاب روي مواد
2- تزريق مواد گوگرد زدا : در اين روش به وسيله لوله هاي گرافيتي مواد گوگرد زدا را به صورت پودر به همراه گاز هاي خنثي مانند نيتروژن و آرگون به مذاب اضافه مي كنند اين روش معمولا در تنارژ هاي بالا استفاده مي شود.
3- تزريق از كف پاتيل : در اين روش از پاتيل هاي مخصوصي استفاده مي شود كه در اين پاتيل ها لوله هايي در كف پاتيل تعبيه شده و مواد گوگرد زدا را همراه با گاز خنثي مي توان از طريق اين لوله هاي به مذاب تزريق كرد .
4- روش پاتيل لرزان : در اين روش مواد گوگرد زدا را در كف پاتيل قرار داده و مذاب آماده شده را روي مواد مي ريزند سپس پاتيل را روي پايه هايي قرار داده و با انجام حركت نوساني تلاطم مورد نياز جهت واكنش مواد گوگرد زدا با مذاب را فراهم مي شود
مرحله سوم : افزايش مواد كربن ده به مذاب :
به علت آن كه در صنعت استفاده از قراضه ها باعث پايين آمدن درصد كربن در مذاب مي شود به همين دليل اين روش يكي از مهمترين مراحل توليد به شمار مي آيد
انواع مواد كربن ده :
1- گرافيت مصنوعي : كه اين تركيب تا حدود 99 درصد كربن دارد
2- گرافيت طبيعي : كه در دو نوع پركربن و كم كربن موجود است . نوع كم كربن آن داراي 80 تا 84 درصد كربن و نوع پر كربن آن داراي 84 تا 87 درصد كربن مي باشد
3- كك متالوژيكي : كه تا حدود 88 درصد كربن دارد
4- كك نفتي كلسينه شده : اين تركيب در صنايع نفتي توليد شده كه تا حدود 99 درصد كربن دارد
5- كك نفتي غير كلسينه : كه تا حدود 92 تا 97 درصد كربن دارد .
شرايط اضافه كردن مواد كربن ده :
1-تماس مواد كربن ده بامذاب : مواد كربن ده بايد با مذاب تماس پيدا كنند زيرا دانسيته يا حجم مخصوص اين مواد پايين تر از مذاب بوده و نتيجتا در بالاي مذاب به همراه سرباره باقي مي مانند لذا بايد تلاطم مذاب در هنگام اضافه كردن مواد كربن ده زياد باشد
2- ايجاد اتمسفر احيايي قوي در داخل كوره : اگر اتمسفر اكسيدي باشد باعث سوختن واكسيد شدن كربن مي شود معمولا اگر كوره اگر شعله اي باشد مي توان با تنظيم شعله محيط احيايي را به وجود آورد به همين خاطر سعي مي شود كه از اتمسفر احيايي يا مايل به خنثي در ذوب ريزي استفاده شود .
3- درجه حرارت كوره بايد مناسب باشد : درجه حرارت 1330 تا 1340 بهترين درجه حرارت براي استفاده كردن مواد اكسيدي مي باشد
4- مقدار سيليسيم بايد كمتر از 1.8 % باشد : ميزان زياد سيليسيم در مذاب باعث كاهش بازيابي كربن در مذاب مي شود لذا مواد كربن ده را قبل از تلقيح به مذاب اضافه مي كنند
مرحله چهارم تلقيح مذاب چدن :
به اضافه كربن مواد معيني به مذاب چدن كه داراي اثر گرافيت زايي بوده و اين مرحله قبل از تخليه مذاب در محفظه قالب به مذاب اضافه مي شود را تلقيح گويند كه هر چه اختلاف زمان بين تخليه مذاب تا تلقيح مذاب كمتر باشد تاثير عناصر تلقيح بيشتر خواهد بود
اثرات تلقيح
1- تعداد هسته ها: در مذاب افزايش مي يابد كه اين امر باعث ريز شدن شبكه كريستالي و دانه هاي مذاب مي شود .
2- ريز شدن گرافيت ها
3- توزيع يكنواخت گرافيت
4- كاهش عمق منطقه سمانتيته شده يا سفيد شده
مجموع اين چهار عامل باعث افزايش خواص مكانيكي چدن مي شود و همچنين قابليت ماشين كاري و تراشكاري چدن را افزايش داده و حفرات انقباضي قطعات چدني را كاهش مي دهد .
علت كاهش حفرات انقباضي افزايش ميزان رسوب گرافيت افزايش درصد سيليسيم مي باشد كه اين امر موجب افزايش حجم بيشتر در مرحله رسوب گرافيت مي شود لذا هم پوشاني حفرات انقباضي در اين مرحله به وجود مي آيد .
انواع مواد تلقيحي :
1- فروسيليس: معمولا فرو سيليس داراي 75% آهن و 1 تا 2 درصد آلومينيم و 0.2 تا 1% كلسيم مي باشد در صنعت فروسيليس بهترين عنصر تلقيحي است كه مورد استفاده قرار مي گيرد . ابعاد مورد استفاده ان از 3 تا 10 ميليمتر مي باشد كه ابعاد كمتر از اين ميزان باعث تلفات عنصر تلقيحي مي شود و ابعاد بيشتر نيز باعث تلفات حرارتي شده ميزان مصرف عنصر تلقيح در مذاب در حدود 0.6 تا 1.2% مي باشد
2- سيليكات كلسيم
3- گرافيت با خلوص بالا
4- زيركنيم سيليسايد
5-تيتانيم: كه در موارد خاص استفاده مي شود .
روش اضافه كردن مواد تلقيحي به مذاب :
1- اضافه كردن مواد تلقيحي به پاتيل
2- تزريق مواد تلقيحي با استفاده از لوله هاي گرافيتي
3- تزريق از كف با استفاده از گاز خنثي
4- اضافه كردن در ناودان خروجي مذاب در كوره
5- اينمولت ( درون قالبي)
در اين روش مواد تلقيحي در داخل سيستم راهگاهي قرار داده شده و مذاب با حركت در سيستم راهگاهي و عبور از روي موادتلقيحي عمليات تلقيح را انجام مي دهند راندمان دراين روش بالا بوده و علت اين امر فاصله زماني كم بين تلقيح و ريخته گري مذاب مي باشد .
ويژگي هاي مواد تلقيحي :
1- به آساني وارد مذاب شده و با مذاب تركيب شود و كمترين ناسازگاري را با مذاب داشته باشد .همچنين باعث ايجاد مواد ناخواسته در مذاب نشود .
2- با اضافه كردن كمترين مواد تلقيحي بيشترين اثر تلقيح را داشته باشيم .
3- كمترين پسماند را داشته باشيم و جدا شدن پسماند از مذاب به راحتي صورت گيرد .
4- حساسيت نسبت به سطح مقطع حداقل باشد : هر چه در ضخامت هاي بيشتر چدن سفيد به دست آيد به اين معني است كه حساسيت به سطح مقطع بيشتر است .
روش كنترل تاثير تلقيح :
كنترل تاثير تلقيح با استفاده از گوه هاي استاندارد انجام مي شود .
گوه هاي مورد استفاده در تلقيح طبق استاندارد ASTM به هشت نوع تقسيم بندي مي شود كه به ترتيب حروف الفباي انگليسي به نام هاي A,B,C,D,E,F,G,H ناميده مي شوند
انواع گوه بر اساس استاندارد ASTM قاعده گوه ارتفاع گوه طول گوه
A يك /چهارم اينچ هفت /شانزدهم اينچ دو/چهارم اينچ
B يك /دوم اينچ هشت/هفتم اينچ 4 اينچ
C
D
E
F
G
H سه اينچ هشت و يك دهم /دوم اينچ هشت اينچ
روش استفاده از گوه :
گوه را پس از قالب گيري از داخل قالب خارج كرده و پس از سرد شدن تا حدود 600 درجه سانتيگراد گرم مي كنيم تا گوه به رنگ خرمايي سوخته تبديل شود سپس گوه را از مقطع نازك وارد آب مي كنيم حال گوه را از قسمت وسط برش داده و از روبه رو به آن نگاه مي كنيم گوه داراي سه منطقه مي شود كه منطقه اول منطقه چدن سفيد منطقه دوم چدن ابلق كه مخلوطي از چدن سفيد و خاكستري است ديده مي شود و در نهايت منطقه سوم چدن خاكستري مورد رويت مي باشد .
نكته در نمودارn حداقل ضخامتي است كه چدن براي خاكستري شدن نياز دارد .
روش توليد قطعات با چدن خاكستري :
1- توليد قطعات در قالب هاي ماسه اي تر – خشك – CO2 – پوسته اي – قالب هاي فلزي
نكته : در ريخته گري چدن هاي خاكستري بهترين و عمومي ترين روش ريخته گري در قالب هاي ماسه اي تر مي باشد كه در اين روش مخلوط قالب گيري شامل ماسه چسب و مواد سلولزي (ارد حبوبات و پودر زغال سنگ مي باشد )
نكته : در ريخته گري قطعات كوچك پودر زغال استفاده شده بين 6 تا 3 درصد باشد همچنين در توليد قطعات بزرگ از 6 الي 7 درصد پودر زغال استفاده مي شود . كه اين امر باعث كاهش ماسه سوزي و همچنين افزايش ديرگدازي و افزايش كيفيت سطحي قطعه مي شود و نيز مانع از انبساط ماسه در فرآيند ذوب ريزي خواهد شد .
2- روش ماسه خشك : اين روش نسبت به ماسه اي تر داراي دقت و كيفيت بالاتري مي باشد همچنين مك و حفرات گازي در اين روش كمتر به وجود مي آيد.
نكته: در اين روش سطح داخلي قالب بين 1 تا 12 ميليمتر خشك بايد شود .
روش CO2 : در اين روش از ماسه سيليسي استفاده مي شود و چسب مورد استفاده در اين روش چسب سيليكات سديم مي باشد كه اين چسب با دمش گاز CO2 ايجاد سيليس كرده كه اين روش موجب چسبيدن ذرات ماسه به هم مي شود . اين روش داراي دقت ابعادي بالاتر و تراشكاري كمتر و عدم نياز به درجه در مرحله ريخته گري مي باشد .
Na2SiO3+CO2=NaCO3+SiO2