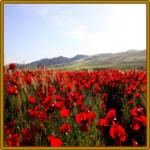
سلام به وب من خوش آمدید دوستان و همراهان عزیز از اینکه مهمان این وب هستید بسیار سپاسگزارم منتظر نظرات سازنده ی شما دوستان هستم
عنوان | پاسخ | بازدید | توسط |
![]() |
1 | 1216 | piskesvat |
![]() |
3 | 2712 | mehran99 |

انواع عملیات حرارتی آلومینیوم :
به منظور حصول خواص دلخواه بر روی آلیاژهای کارپذیر و ریختگی آلومینیوم عملیات ها متفاوتی صورت می گیرد که در زیر به صورت جزیی به آن ها اشاره می شود، برای مطالعه ی بیشتر در این رابطه به کتب نوشته شده در مرجع مراجعه شود.
آنیل(Anneal):
برای آلیاژهای عملیات حرارتی پذیر و همچنین غیر عملیات حرارتی پذیر به منظور حذف تاثیرات ویژه ی مار سرد صورت می گیرد. نسبت نرم سازی آلیاژ وابسته به دما خواهد بود، متناسب با دما زمان لازم برای آنیل می تواند از چندین ساعت در دمای کم به چندین ثانیه در دماهای زیاد تغییر کند.
آنیل کامل (Full Annealing):
بیشترین مقدار شکل پذیری و نرمی، بیشترین شرایط کارپذیر در آلیاژهای آلومینیوم عملیات حرارتی پذیر و یا غیر قابل عملیات حرارتی به وسیله ی عملیات حرارتی آنیل کامل بوجود می آید. در این حالت آلیاژ تحت عملیات تمپر (برگشت) به صورت نرمال کریستال سازی مجدد می شوند.
آنیل جزیی(Partial Annealing) :
آنیل تنش زدایی(Stress Relief Annealing) :
برای آلیاژهای کار شده ی قابل عملیات حرارتی، عملیات آنیل صرف فقط به حذف تاثیرات مرتبط به منحنی کشش منحر می شود، بنابراین ب آلین تنش زدایی تاکید می شود. عملیات آنیل تعریف شده برای تنش زدایی آلومینیوم درجه حرارت های حدود 345 درجه سانتی گراد را به کار می گیرند و البته این امر ممکن است فقط به اصلاح و بهبود کریستال سلزی جزیی و یا کامل نتیجه دهد.
آنیل مربوط به ریخته گری ها(Annealing of Casting):
عملیات آنیل مربوط به ریخته گری ها عموما برای 2 تا 4 ساعت و در درجه حرارت 315 تا 345 درجه ی سانتی گراد انجام می شود.
پیر سازی رسوبی (Precipitation Hardening) :
از این عملیات برای افزایش استحکام و سختی آلیاژهای آلومینیوم ریخته گری و کار شده با مکانیزم سخت سازی رسوبی استفاده می شود.
- حروف مختلفی که بعد از نام آلیاژ قرار می گردد به معنای انجام گرفتن عملیاتی خاص بر روی آن می باشد که در زیر به آن ها اشاره می شود.
F : یعنی هیچ فرآیند اضافی برای سخت کاری و بهبود خواص استحکام آلیاژ انجام نشده است.
O : آنیل یا نرم سازی با گرم کردن و سرد کردن به صورت کنترل شده.
H : سخت کاری کرنشی یا کار سخت شده با روش کار سرد.
T : محصول تحت عملیات حرارتی پیر سختی و گاها در عملیات کار سرد قرار گرفته است.
علائم اختصاري عمليات حرارتي آلومينيم :
T1 : به طور طبیعی پیر سازس می شود. محصول از دمای بالای شکل دهی سرد می شود و پس از یک جالت اساسا پایدار به طور طبیعی پیر سازی می شود.
T2 : سرد شده از یک فرآیند شکل دهی با دمای بالا+کار سرد+پیرسازی طبیعی در یک شرایط اساسا پایدار
T3 : عملیات حرارتی انحلال + کار سرد + پیرسازی طبیعی در یک شرایط اساسا پایدار
T4 : عملیات حرارتی انحلال + پیرسازی طبیعی در یک شرایط اساسا پایدار
T5 : سرد شده از یک فرآیند شکل دهی با دمای بالا + پیرسازی مصنوعی
T6 : عملیات حرارتی انحلال + پیرسازی مصنوعی
T7 : عملیات حرارتی انحلال + پایدار سازی
T8 : عملیات حرارتی انحلال + کار سرد + پیرسازی مصنوعی
T9 : عملیات حرارتی انحلال+ پیرسازی مصنوعی + کار سرد
T10 : سرد شده از یک فرآیند شکل دهی با دمای بالا + کار سرد + پیرسازی مصنوعی
عناصر و تاثیر آن ها در آلیاژهای آلومینیوم :
به طور کلی لغت آلیاژ به معنی افزودن یک یا چند عنصر یا ترکیبی از آنها به فلز پایه برای دستیابی به یکسری خواص خاص میباشد.تغییر خواص ناشی از افزودن این عناصر بسته به نوع عنصر پایه و عناصر آلیاژی اضافه شده میتواند منحصرا وابسته به یک عنصر یا ترکیبی از عناصر اضافه شده باشد.
از آنجا که استحکام و سختی فلز خالص همیشه کمتر از آلیاژهای آن فلز می باشد عموما از فلزات به صورت آلیاژی استفاده میشود و از فلز خالص معمولا در کاربردهای ویژه استفاده میشود.آلومینیوم با درارا بودن آلیاژهای مختلف با ترکیب و خواص متفاوت در محدوده کاربردی فراوانی توانسته است ایفای نقش کند.
معمولا هرچه فلز خالص تر باشد استحکام آن کمتر ولی نرمی و پایداری شیمیایی آن زیادتر است.اگرچه آلیاژهای آلومینیوم دارای استحکامی بیشتر از آلومینیوم خالص هستند.
اما این استحکام برای کاربردهایی که تحت تنش های بالا هستند کافی نیست و لذا این آلیاژها نیز نیاز به افزایش استحکام بیشتری دارند و به همین دلیل از روش های مختلف استحکام آنرا افزایش میدهند.
این روش ها عبارتند از:
۱-کرنش سختی (کار سختی) : کار سختی اصطلاحی است که برای مفهوم سخت شدن و افزایش استحکام فلز دراثر فرایندهای کار سرد مثل:نورد،کشش،پرس و … عنوان میگردد.
۲-عملیات حرارتی انحلال-پیر سختی:یک نوع عملیات حرارتی است که بر روی آلیاژهای آلومینیوم انجام میپذیرد و باعث افزایش استحکام و سختی قطعه میشود.
هریک از این روش ها از طریق مکانیزم خاص خود استحکام فلز را افزایش می دهند.ترکیبی از عملیات حرارتی پیر سختی و آلیاژسازی توانسته است استحکام آلومینیوم را به حدی برساند که در برخی موارد جایگزین فولاد شود.قبل از بررسی مشخصات آلیاژهای آلومینیوم لازم است تا تاثیر هر عنصر به صورت منفرد بر خواص فلز پایه آلومینیوم بررسی گردد.
تاثیر عناصر آلیاژی :
هر یک از عناصر آلیاژی به تنهایی یا در حضور سایر عناصر خواص ویژه ای را به آلومینیوم می دهد.تاثیر هر یک از عناصردرحالتی که به تنهاییبه فلز پایه آلومینیوم افزوده گردد را به صورت زیرمیتوان دستهبندی کرد:
1) مس (CU) :
بیشترین مقدار مس که در آلیاژهای آلومینیوم مورد استفاده قرار گرفته است حدود ۴ تا ۱۰ درصد میباشد.مس باعث بهبود استحکام و سختی در حالت ریختگی و عملیات حرارتی شده می گردد.آلیاژهای دارای ۴ تا ۶ درصد مس،بسیار عملیات حرارتی پذیرند.مس عموما مقاومت به خوردگی و در برخی ترکیبات شیمیایی حساسیت به خوردگی ناشی از تنش را کاهش می دهد.افزودن مس مقاومت به ترک گرم و قابلیت ریخته گری را کاهش می دهد.
2) سیلیسیم (Si) :
سیلیسیم باعث بهبود شرایط ریخته گری میشود و شدیدا سیالیت،مقاومت به ترک گرم و خاصیت مذاب رسانی آلومینیوم را بهبود میبخشد.خانواده آلیاژهای آلومینیوم-سیلیسیوم کاربرد بسیار زیادی در صنعت دارد و به صورت یوتکتیک و هیپو یوتکتیک و هایپر یوتکتیک تا ۲۵ درصد سیلیسیم مصرف میشوند. به طور کلی مطلوب ترین مقدار سیلیسیم برای قطعات ریختگی در فرایندهای توام با سرعت سرد شدن آهسته نظیر ریخته گری در ماسه ، ریخته گری دقیق و نیز ریخته گری گچی بین ۵-۷ درصد،بین قالب های دائمی بین ۷-۹ درصد و در ریخته گری تزریقی بین ۸-۱۲ درصد میباشد.
3) منیزیم (mg) :
این عنصر اساس بهبود استحکام و سختی در آلیاژهای آلومینیوم-سیلیسیم عملیات حرارتی پذیر میباشد و عموما در آلیاژهای آلومینیوم – سیلیسیم به همراه سایر عناصر نظیر مس و نیکل به همین منظور مورد استفاده قرار میگیرد.
آلیاژآلومینیوم-سیلیسیم دارای منیزیمی بین ۰٫۰۷ تا ۰٫۴ درصد هستند.آلیاژهای ۲ تایی آلومینیوم منیزیم به طور گسترده در کاربرد هایی که نیاز به سطح تمام شده روشن و مقاومت خوردگی و همچنین ترکیبی از استحکام و شکل پذیری دارند مورد استفاده قرار میگیرد.
4) روی (zn) :
روی به تنهایی اثر چندان مفیدی بر آلومینیوم ندارد.ولی همراه با مس و یا منیزیم باعث ایجاد خواص جالب عملیات حرارتی و پیر سختی طبیعی میگردد.روی بیشتر در ترکیبات شیمیایی آلیاژهایی که از طریق دایکست و ریخته گری ثقلی تهیه میشوند،یافت میشود.
5) قلع (sn) :
این عنصر به طور موثر خاصیت ضد اصطکاکی را بهبود میبخشد و بنابراین برای کاربردهای یاتاقانی مفید میباشد.آلیاژهای ریختگی ممکن است تا ۲۵ درصد قلع داشته باشند.افزایش قلع همچنین باعث بهبود خاصیت ماشینکاری می شود.قلع ممکن است در بعضی آلیاژها عمل رسوب سختی را تحت تاثیر قرار دهد.
6)سرب (pb) :
وجود سرب در آلیاژهای ریختگی آلومینیوم در مقادیر بیش از ۰٫۱ درصد باعث بهبود خاصیت ماشین کاری میشود.
7) آهن (Fe) :
این عنصر مقاومت به ترک گرم را بهبود داده و چسبیدن قطعه به قالب یا به عبارتی جوش خوردن قطعه به قالب در ریخته گری تزریقی را کاهش میدهد.افزایش زیاد آهن باعث کاهش فرم پذیری میشود.آهن با سایر عناصر در مذاب واکنش داده و باعث ایجاد ترکیبات بین فلزی و یا فازهای غیر محلول در مذاب آلومینیوم میشود که وجود این فازها استحکام در دماهای کاربردی بالا را بهبود میبخشند.افزایش آهن که باعث فازهای غیر محلولی میگردد موجب کاهش خاصیت سیالیت و مذاب رسانی میشود.آهن همراه با سایر عناصر نظیر منگنز و کروم ترکیبات بین فلزی پیچیده و یا لجن تولید می کند.
8)منگنز (Mn) :
عنصر منگنز در مقادیر کم برای کنترل اثر تخریبی آهن به صورت فازهای شکننده و ترد به کار میرود.مقدار منگنز در حدود نصف درصد آهن می باشد.منگنز به عنوان عنصر آلیاژی در ترکیبات آلیاژهای کار پذیر به کار میرود.شواهدی وجود دارد مبنی بر اینکه کسر حجمی زیاد6MnAl در آلیاژهای حاوی بیش از ۵۰% منگنز به طور موثری بر سلامت قطعات ریختگی تاثیر میگذارد.
9) کروم (Cr) :
افزودن کروم باعث ایجاد ترکیبات بین فلزی 7CrAl میشود و چون این ترکیبات حلالیت بسیار کمی در حالت جامد دارند،از رشد دانه جلوگیری می کنند.کروم در برخی از آلیاژهای مقاومت به خوردگی را بهبود داده و در مقادیر بالاتر حساسیت به سریع سرد شدن را افزایش می دهد.
10)نیکل (Ni) :
این عنصر همراه با مس مقاومت در درجه حرارت بالا را افزایش داده و همچنین ضریب انبساط حرارتی را کاهش می دهد.
11)فسفر (p) :
فسفر به صورت AlP3 باعث جوانه زنی و ریز شدن فاز سیلیسیم اولیه در آلیاژهای هایپر یوتکتیک آلومینیوم-سیلیسیم می شود.فسفر اثر اصلاح سازی سدیم و استرانسیم را از بین میبرد.
12)تیتانیم (Ti) :
این عنصر برای ریز کردن ساختارذدر آلیاژهای ریختگی آلومینیوم به کار می رود و معمولا همراه با مقادیر کمی از بور استفاده میشود.
13)آنتیموان (Sb) و سدیم (Na) :
هردوی این عناصر در مقادیر کم در حدود ۰٫۰۵ درصد جهت اصلاح و بهسازی سیلیسیم در آلیاژهای آلومینیوم-سیلیسیم بکار میرود.
عملیات حرارتی آلیاژهای آلومینیوم :
در آلیاژهای آلومینیوم ، عملیات حرارتی برای آلیاژهای معینی بکار می رود که که می توان با آن استحکام و سختی را افزایش داد.این آلیاژها را عملیات حرارتی پذیر Heat treatable می گویند.در برابر این آلیاژهایی وجود دارند مه که با سیکل های حرارتی و سرد کردن نمی توان استحکام آنها را افزایش داد.برای مشخصکردنوتمییزقایلشدنباآلیاژهایقبلی،اینآلیاژهایراعملیاتحرارتی ناپذیر(None-heat treatable)می نامند.تنها روش استحکام این آلیاژها، انجام کار سرد است.حرارت دادن هر دو نوع آلیاژ تا دمای مشخص برای افزایش داکتیلیتی و کاهش استحکام (آنیل)متداول بوده و با توجه به درجه نرم شدن ، واکنش هاس متالورژیکی مختلفی در ریزساختار رخ می دهند
خاصیت بسیار مهم در سیستم های آلیاژی رسوب سختی شونده ، وابستگی قابلیت انحلالی تعادلی به دما است که با افزایش درجه حرارت ، قابلیت انحلالی نیز افزایش می یابد.این رفتار در اکثر سیستم های دوتایی Al مشاهده می شود هرچند که در برخی از آلیاژهای آن رسوب سختی کمتری دیده می شوند که همان آلیاژهای عملیات حرارتی ناپذیر را تشکیل می دهند.به عنوان مثال، در آلیاژهای با سیستم دوتایی Al-Si,Al-Mn ، خواص مکانیکی بعد از عملیات حرارتی افزایش نمی یابد با این وجود رسوبات قابل توجهی تشکیل می شود
رابطه دما – انحلال برای سیستمهای رسوب سختی Al-Cu توضیح داده میشود. قابلیت انحلال مس در آلومینیوم با افزایش دما افزایش می یابد.(0.25 % در دمای 250 C به حداکثر 5.65 % در 548 C دمای یوتکیتیک) در آلیاژهای Al-Cu که دارای 0.2-5.6 % مس هستند،دو حالت تعادلی مجزا وجود دارند.در دماهای بالای منحنی solvus مس کاملا حل می شودو اگر در این دما نگه داشته شود و با فرض کافی بودن زمان ، مس کاملا وارد محلول جامد می شود.و در دماهای کمتر از solvus حالت تعادلی از دو فاز تشکیل می شود.محلول جامد α و فاز ترکیب بین فلزی Ө(Al2Cu) . اگر چنین آلیاژی که در دمای بالای solvus کاملا بصورت محلول جامد است تا مای زیر این دما سرد شود محلول جامد فوق اشباعی تشکیل می شود که در این حالت آلیاژ شرایط تعادلی دو فازی را دنبال می کند و فاز دوم تمایل دارد که با رسوب در حالت جامد تشکیل شود.
آلیاژهای غیر قابل عملیات حرارتی آلومینیوم :
در میان آلیاژهای کار پذیر آلومینیوم، آلیاژهای آلومینیم -منگنز (xxx 3)و آلیاژهای آلومینیوم-منیزیم (xxx 5) قابلیت انجام عملیات حرارتی را ندارند.
آلیاژهای آلومینیم –منگنز :
حلالیت منگنز در آلومینیم 1.82 درصد است ولی مقدار منگنز در آلیاژ های آلومینیوم برابر با 1.25 درصد است. علت این اختلاف حضور آهن به عنوان ناخالصی است که باعث کاهش حلالیت می شود. تنها آلیاژ پر مصرف آلومینیم – منگنز، آلیاژ 3003 است. افزودن منگنز به آلومینیوم از طریق تشکیل محلول جامد و توزیع ظریف رسوب های نامحلول، استحکام آن را افزایش می دهد. افزدون یک درصد منیزیم منجر به افزایش بیشتر استحکام می شود. آلیاژ های گروه 3xxxدارای استحکام متوسط، انعطاف پذیری بالا و مقاومت خوردگیمطلوبی هستند. این آلیاژ ها برای ساخت قوطی های نوشابه، وسایل آشپزخانه و پخت و پز به کار می روند.
آلیاژهای آلومینیم-منیزیم :
آلومینیم و منیزیم در محدوده وسیعی از ترکیب شیمایی تشکیل محلول جامدمی دهند و آلیاژ های کارپذیری تولید می کنند که حاوی 0.8 الی 5 درصد منیزیم است. مستحکم ترین آلیاژ این گروه 5456 است که استحکام کششی آن برابر با 310 مگا پاسکال است. اگر در این آلیاژها مقدار منیزیم بیش از 4-3 درصد باشد، فاز βیا Mg5Al8 روی مرز دانه ها و نوارهای لغزشی رسوب می کند و همین موضوع منجر به خوردگی بین دانه ایو ایجاد ترک در اثر خوردگی تنشیمی شود. افزودن کرومو منگنز می تواند از این مسئله جلوگیری کند. این آلیاژ ها در بدنه کامیون ها، مخازن بزرگ حمل بنزین، شیر و دانه های غلات، مخازن تحت فشار(به خصوص در دما های پایین) ، بدنه قایق های کوچک و کشتی های اقیانوس پیما مورد استفاده قرار می گیرند.
آلیاژهای عملیات حرارتی پذیر آلومینیوم :
در میان آلیاژهای کار شده آلومینیم، آلیاژهای سری 2xxx، 6xxx،7xxx قابلیت انجام عملیات حرارتی را دارند.
آلیاژهای آلومینیم-مس و آلومینیم-مس-منیزیم :
تغییراتی که در حین پیر کردن آلیاژهای آلومینیوم - مس رخ می دهد، بسیار بیشتر از سایر آلیاژ ها مورد توجه قرار گرفته است، اما تنها چند آلیاژ تجاری بر پایه این سیستم وجود دارد. آلیاژ 2011 قابلیت ماشین کاری خوبی دارد ولی امروزه آلیاژ 2219 به علت خواص مناسب تر، جای آلیاژ 2011 را گرفته است. آلیاژ 2219 دارای خواص کششی بالا، استحکام خزشی خوب و چقرمگی زیادی است.
آلیاژهای آلومینیم - مس - منیزیم در سال 1906، به طور اتفاقی در برلین ساخته شدند و تحقیقات انجام شده روی این آلیاژ منجر به پیدایش آلیاژ دورآلومین شد. معمولا این آلیاژ ها و سایر آلیاژ های گروه 2xxx به وسیله روش نوردی با آلومینیم یا آلیاژ آلومینیم - روی پوشش داده می شوند تا مقاومت به خوردگی مطلوبی را ایجاد کنند. در یک استحکام کششی برابر، آلیاژهای گروه 2xxx از آلیاژ های گروه 7xxx چقرمگی شکست پایین تری را نشان می دهند. دلیل این مسئله، اندازه بزرگ ترکیبات بین فلزی در آلیاژ های 2xxx است. با کاهش مقادیر آهن، سیلیسم و مس، چقرمگی شکست و انعطاف پذیری بهبود می یابد. این آلیاژ ها در هواپیما و صنایع اتومبیل سازی به کار می روند.
آلیاژهای آلومینیم-منیزیم-سیلیسیم :
آلیاژهای آلومینیم - منیزیم - سیلیسیم به عنوان آلیاژ های ساختمانی به کار می روند. این آلیاژ ها دارای خواص جوش پذیری، مقاومت در برابر خوردگی و خوردگی تنشی هستند. این آلیاژ ها بیشتر به صورت اکسترود شده به کار می روند. آلیاژ های این گروه به سه دسته تقسیم بندی می شوند:
1- آلیاژهایی با مقدار منیزیم و سیلیسیم بین 0.8 تا 1.2 درصد که به آسانی اکسترود می شوند. محصول خروجی از اکستروژن قابلیت کوئنچ دارد و نیاز به عملیات محلول سازی جداگانه نیست.
2- آلیاژهای دو دسته دیگر حاوی مقادیر منیزیم و سیلیسم بیش از 1.4 درصد هستند. این آلیاژ ها پس از اکسترود شدن به عملیات محلول سازی و کوئنچ نیاز دارند.
3- آلیاژهای دسته سوم دارای مقدار سیلیسمی بیش از مقدار مورد نیاز برای تشکیلMg2Siهستند. افزایش مقدار سیلیسم منجر به ریز شدن اندازه ذرات Mg2Siو رسوب سیلیسم می شود و به پیرسختی کمک زیادی می کند.
آلیاژهای آلومینیم-روی-منیزیم و آلومینیم-روی-منیزیم-مس :
آلیاژهای آلومینیم - روی - منیزیم در میان کلیه آلیاژ های آلومینیم بیشترین پتانسیل پیرسختی را دارند. در آلیاژ های پر استحکام این گروه از مس به مقدار کمتر از 0.3 درصد، برای افزایش مقاومت به خوردگی تنشی استفاده می شود. آلیاژ هایی که فاقد مس یا دارای مقادیر اندکی مس هستند، به آسانی جوشکاری می شوند. این آلیاژ ها در دمای محیط به طور قابل ملاحظه ای پیرسخت شده و محدوده وسیع دمایی برای عملیات محلول سازی آن ها وجود دارد. بنابراین در هنگام جوشکاری، استحکام آلیاژ بازیابی می شود و نیاز به عملیات حرارتی دیگری نیست. آلیاژهای آلومینیم - روی - منیزیم در ابتدا برای ساخت پل های نظامی سبک مورد استفاده قرار گرفتند. امروزه برای کنترل ساختار این آلیاژها از عناصر کروم، منگنز و زیرکونیوم استفاده می شود. آلیاژهای آلومینیم - روی - منیزیم - مس بیشترین میزان پیرسختی را از خود نشان می دهند. نیاز صنایع نظامی به استفاده از آلیاژ های هواپیمایی که نسبت استحکام به وزن آن ها بالا باشد، در نهایت منجر به تولید آلیاژهای گروه Al-Zn-Mg-Cuشد. آلیاژ 7075 شناخته شده ترین آلیاژ این گروه است.
منابع :
گردآوری شده توسط دپارتمان پژوهشی شرکت پاکمن
Polmear,I. J. Light Alloys: From traditional Alloys to Nanocrystals, Butterworth-Heinemann, 2006.
Smith, W. F.Structure and properties of engineering alloys, McGraw-Hill, 1993.
دانلود بصورتpdf ، word